Tubular Heat Exchange
a technology of heat exchange and tubular structure, which is applied in the direction of indirect heat exchangers, machines/engines, lighting and heating apparatus, etc., can solve the problems of difficult and costly formation of exotic materials into complex shapes such as annular heat exchangers, and the environment of extreme temperature environments
- Summary
- Abstract
- Description
- Claims
- Application Information
AI Technical Summary
Benefits of technology
Problems solved by technology
Method used
Image
Examples
Embodiment Construction
[0031]In one embodiment, the invention relates to a heat exchanger assembly such as a regenerator assembly for use with a thermodynamic cycle-based device such as a Stirling cycle machine. The heat exchanger assembly includes an acceptor heat exchanger, a regenerator heat exchanger, and a rejector heat exchanger and one or more assemblies. Typically, one heat exchanger assembly formed from one or more tubes is used. For example, a tube can be molded or formed to include a chamber or bulge having a larger diameter relative to the segments of the tube on either side of such a chamber or bulge. Alternatively, a first tube and a second tube can connect to a third tube or canister. A regenerator material is disposed in such a chamber or canister in one embodiment. Thus, one or more tubes or canisters can be connected in series.
[0032]Embodiments of the invention relate to a heat exchanger assembly that includes one or more tubes connected in series. As part of one embodiment, a regenerato...
PUM
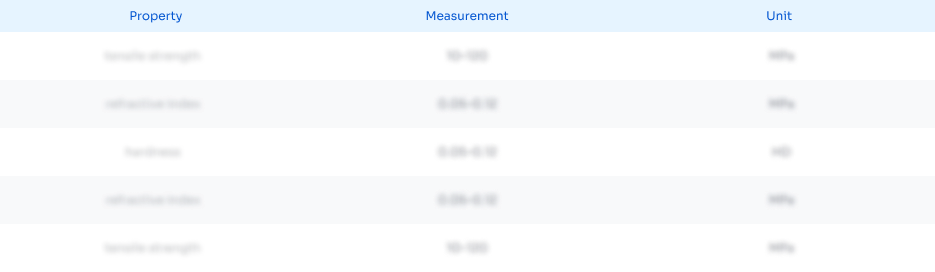
Abstract
Description
Claims
Application Information

- R&D
- Intellectual Property
- Life Sciences
- Materials
- Tech Scout
- Unparalleled Data Quality
- Higher Quality Content
- 60% Fewer Hallucinations
Browse by: Latest US Patents, China's latest patents, Technical Efficacy Thesaurus, Application Domain, Technology Topic, Popular Technical Reports.
© 2025 PatSnap. All rights reserved.Legal|Privacy policy|Modern Slavery Act Transparency Statement|Sitemap|About US| Contact US: help@patsnap.com