System for Controlling Torque Distribution
a torque distribution and torque technology, applied in the direction of interengaging clutches, couplings, gearing, etc., can solve the problems of adversely affecting the reliance on indirect determination of traction loss, and the acceleration sensor not directly detecting the loss of traction, so as to improve the cruising stability of the vehicl
- Summary
- Abstract
- Description
- Claims
- Application Information
AI Technical Summary
Benefits of technology
Problems solved by technology
Method used
Image
Examples
Embodiment Construction
[0020]Referring to the drawings, a description will be made with regards to preferred embodiments of a torque distribution control system according to the present invention.
[0021]FIG. 1 shows a first preferred embodiment of the present invention. A drive source 24, which can include a transmission and an engine (not shown), generates torque and transfers the torque to a first shaft portion 1A when a primary clutch (not shown) is engaged. The torque causes the first shaft portion 1A to rotate about its longitudinal axis. In a torsion unit 3, deformable elastic elements 4 connect the first shaft portion 1A to a housing 31 located at one end of a second shaft portion 1B. The other end of second shaft portion 1B is mechanically connected to a primary driving axle 2 that is continuously engaged to the drive source, the primary driving axle 2 equipped with rotatably mounted primary driving wheels 32. As the first shaft portion 1A rotates, torque is transferred to the second shaft portion ...
PUM
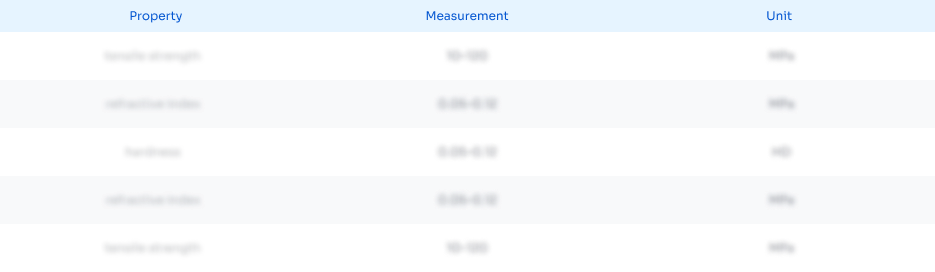
Abstract
Description
Claims
Application Information

- R&D
- Intellectual Property
- Life Sciences
- Materials
- Tech Scout
- Unparalleled Data Quality
- Higher Quality Content
- 60% Fewer Hallucinations
Browse by: Latest US Patents, China's latest patents, Technical Efficacy Thesaurus, Application Domain, Technology Topic, Popular Technical Reports.
© 2025 PatSnap. All rights reserved.Legal|Privacy policy|Modern Slavery Act Transparency Statement|Sitemap|About US| Contact US: help@patsnap.com