Turbine engine component for adaptive cooling
a technology of adaptive cooling and turbine engine, which is applied in the direction of liquid fuel engines, marine propulsion, vessel construction, etc., can solve the problems of negative side effects on the overall performance of the compressor and/or the turbine section, material may still oxidise during operation, and the time of operation can be stretched further, and the downtime may be avoided. only marginal performance loss
- Summary
- Abstract
- Description
- Claims
- Application Information
AI Technical Summary
Benefits of technology
Problems solved by technology
Method used
Image
Examples
Embodiment Construction
[0034]Referring now to FIG. 1, one half of an aerofoil 1 of a turbine is shown in a perspective view as seen from the inside of the aerofoil 1. The second half of the aerofoil 1 that would disallow the view to the inside of the aerofoil 1 is not shown is only indicated by broken and dashed lines.
[0035]The aerofoil 1, for example a guide vane or a blade within a turbine section of a gas turbine engine, represents the turbine engine component as defined in the invention and will be present in a working fluid flow 30 during operation. This working fluid flow 30 is indicated as a double arrow and may be a hot gas provided by a combustion chamber located upstream. The aerofoil 1 has a circumferential wall 2 as a body of turbine engine component and a cavity to allow cooling fluid—a cooling fluid flow 31 is indicated via a further arrow—to cool the wall 2 from the inside and to supply cooling holes (not shown in the figure).
[0036]The wall 2 has a first surface 10 which is exposed, in use,...
PUM
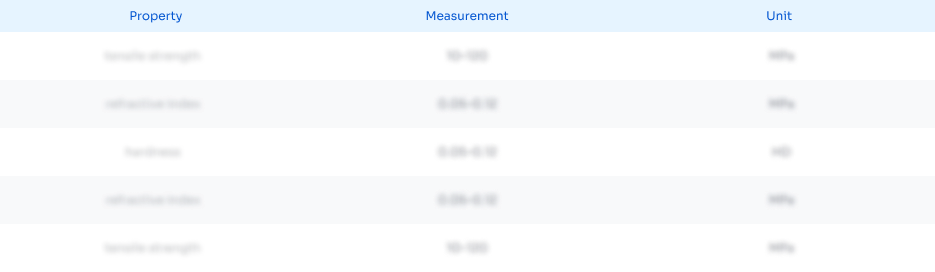
Abstract
Description
Claims
Application Information

- R&D
- Intellectual Property
- Life Sciences
- Materials
- Tech Scout
- Unparalleled Data Quality
- Higher Quality Content
- 60% Fewer Hallucinations
Browse by: Latest US Patents, China's latest patents, Technical Efficacy Thesaurus, Application Domain, Technology Topic, Popular Technical Reports.
© 2025 PatSnap. All rights reserved.Legal|Privacy policy|Modern Slavery Act Transparency Statement|Sitemap|About US| Contact US: help@patsnap.com