Foil container with foil bag chambers which are arranged next to one another
a technology of foil bags and foil containers, applied in the field of foil containers, can solve the problems of high ejection force required for dispensing, and achieve the effect of reducing ejection for
- Summary
- Abstract
- Description
- Claims
- Application Information
AI Technical Summary
Benefits of technology
Problems solved by technology
Method used
Image
Examples
Embodiment Construction
[0024]The foil container 11 according to the present invention and designed for storing a compound and for insertion into a receptacle of a ejection device, not shown, and which is shown in FIGS. 1 and 2, has two foil bag chambers 12 and 16 for compound components of a multi-component compound, which are stored separately from one another, and which foil bag chambers 12 and 16 are arranged next to one another. Further, the foil container 11 has a head 21 with a base plate 22 having, at a contact side 23, a receptacle portion 24 for one end of the foil bag chamber 12 and a receptacle portion 25 for one end of the foil bag chamber 16. A mixer connection 31 with an external thread 32 for the connection of a mixer housing 41 with a mixing element 42 is provided at a side 26 of the base plate 22 located opposite the contact side 23. In the mixer connection 31, there are provided a first outlet opening 33 with a circular clear cross-section defined by a wall 35 facing inward. The compound...
PUM
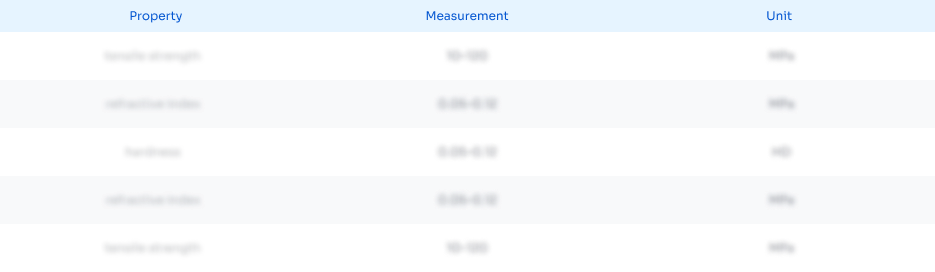
Abstract
Description
Claims
Application Information

- R&D
- Intellectual Property
- Life Sciences
- Materials
- Tech Scout
- Unparalleled Data Quality
- Higher Quality Content
- 60% Fewer Hallucinations
Browse by: Latest US Patents, China's latest patents, Technical Efficacy Thesaurus, Application Domain, Technology Topic, Popular Technical Reports.
© 2025 PatSnap. All rights reserved.Legal|Privacy policy|Modern Slavery Act Transparency Statement|Sitemap|About US| Contact US: help@patsnap.com