Electro-magnetic clamp for gripping a shaft
a technology of magnetic clamping and shaft gripping, which is applied in the direction of rigid shaft couplings, mechanical equipment, filament handling, etc., can solve the problems of high wear and other drawbacks of the type of system, and the complexity of the system is relatively high
- Summary
- Abstract
- Description
- Claims
- Application Information
AI Technical Summary
Benefits of technology
Problems solved by technology
Method used
Image
Examples
Embodiment Construction
[0017] Referring to the Figures, the clamp body 10 comprises a suitable rigid material, such as a metal such as stainless steel or aluminum, or injection-molded plastic. The body includes a central bore 12 for receiving the shaft 14 in a manner which permits the shaft to slide and rotate freely within the bore when the clamp is in the released position. The bore is symmetrical about its elongate axis, with widened cylindrical recesses 16 at each of its opposed, outboard ends to receive a pair of opposed grippers 24, described below. The recesses 16 open to the opposed ends 18 of the body. The base of each recess 16 is inwardly stepped and comprises an annular shoulder 20 for abutting the outer sleeve 22 of a gripper 24, and a recessed pocket 26 to receive the inner sleeve 28 of gripper 24 to permit a degree of axial movement of the inner sleeve 28 relative to the outer sleeve 22 which is fixed in position. Protruding outwardly from opposing positions on either side of the body is a ...
PUM
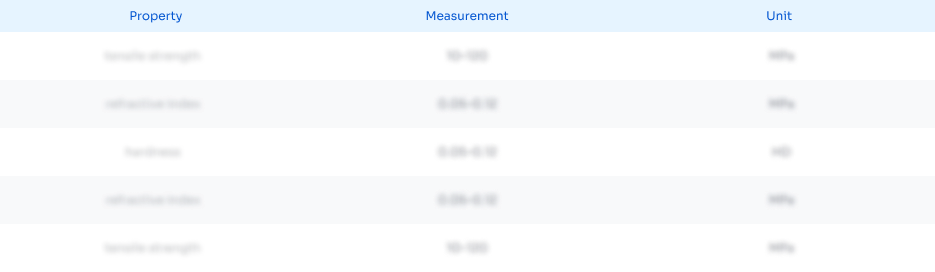
Abstract
Description
Claims
Application Information

- R&D
- Intellectual Property
- Life Sciences
- Materials
- Tech Scout
- Unparalleled Data Quality
- Higher Quality Content
- 60% Fewer Hallucinations
Browse by: Latest US Patents, China's latest patents, Technical Efficacy Thesaurus, Application Domain, Technology Topic, Popular Technical Reports.
© 2025 PatSnap. All rights reserved.Legal|Privacy policy|Modern Slavery Act Transparency Statement|Sitemap|About US| Contact US: help@patsnap.com