Fluid-working machine and operating method
- Summary
- Abstract
- Description
- Claims
- Application Information
AI Technical Summary
Benefits of technology
Problems solved by technology
Method used
Image
Examples
Embodiment Construction
[0029] The machine described in EP-A-0494236 and shown in FIG. 1 can be adapted to provide a machine according to the invention without additional hardware to create a part-stroke mode. The adaptation consists of increasing the functionality and complexity of the microprocessor control algorithms.
[0030] At any one instant there are four possible states for any of the chambers 11: (1) intake from the low-pressure manifold, (2) exhaust to the low-pressure manifold, (3) intake from the high-pressure manifold and (4) exhaust to the high-pressure manifold.
[0031] Let “mode” denote a repeating cyclic sequence of transitions from one of these states to another. There are five distinct modes: full stroke pumping, part stroke pumping, full stroke motoring, part stroke motoring, and idling.
[0032] The difference between full and part stroking modes is the phase angle at which transitions are made from one of these states to the other relative to bottom and top dead centre of piston movement:...
PUM
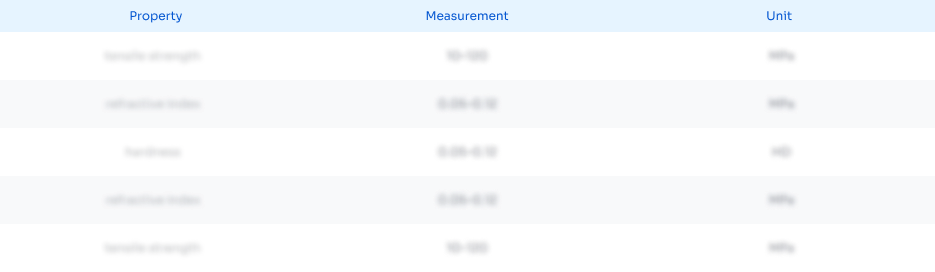
Abstract
Description
Claims
Application Information

- R&D
- Intellectual Property
- Life Sciences
- Materials
- Tech Scout
- Unparalleled Data Quality
- Higher Quality Content
- 60% Fewer Hallucinations
Browse by: Latest US Patents, China's latest patents, Technical Efficacy Thesaurus, Application Domain, Technology Topic, Popular Technical Reports.
© 2025 PatSnap. All rights reserved.Legal|Privacy policy|Modern Slavery Act Transparency Statement|Sitemap|About US| Contact US: help@patsnap.com