Cuff and collar press having asymmetric pleaters
a cuff and collar press and pleater technology, which is applied in the field of clothing articles pressed by apparatus, can solve the problems of not being able to effectively finish the portion of the sleeve the art barrel presser cannot allow the efficient and practical pressing of the shirt cuff, and the portion of the shirt immediately adjacent to the cuff will not be effectively finished. , to achieve the effect of efficient pressing the collar, cuffs and sleeves
- Summary
- Abstract
- Description
- Claims
- Application Information
AI Technical Summary
Benefits of technology
Problems solved by technology
Method used
Image
Examples
Embodiment Construction
[0022] A typical “tube” design collar / cuff press normally presses the collar and both cuffs simultaneously. These prior art designs incorporate a collar press in the center portion of the tube which uses a narrow strip of padding to press only the collar without wrinkling the body of the shirt and two cuff pressing areas (one at each end of the form) to press the cuffs. A preferred embodiment of the present invention modifies this type of cuff and collar press such that the pleats where the end of the sleeve meets the cuff are also pressed. To accomplish this, pleating protrusions are preferably added to each end of the pressing tube. The preferred profile of the pleating protrusions is asymmetrical so that the pleats may be pressed without crushing the rest of the sleeve where it meets the cuff.
[0023] Referring now to FIGS. 1 and 2(a-b), a front and side views of an improved cuff and collar press 2 constructed in accordance with a preferred embodiment of the present invention are ...
PUM
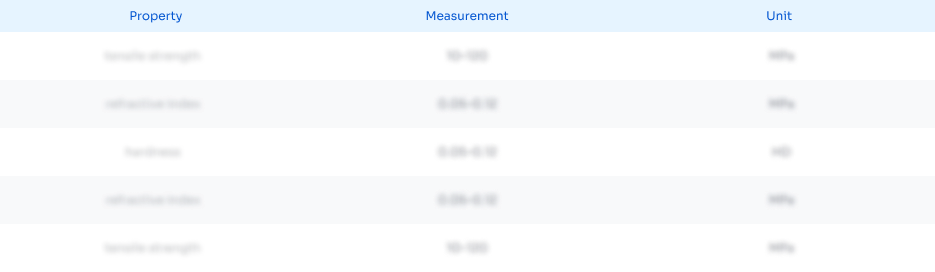
Abstract
Description
Claims
Application Information

- R&D
- Intellectual Property
- Life Sciences
- Materials
- Tech Scout
- Unparalleled Data Quality
- Higher Quality Content
- 60% Fewer Hallucinations
Browse by: Latest US Patents, China's latest patents, Technical Efficacy Thesaurus, Application Domain, Technology Topic, Popular Technical Reports.
© 2025 PatSnap. All rights reserved.Legal|Privacy policy|Modern Slavery Act Transparency Statement|Sitemap|About US| Contact US: help@patsnap.com