Aircraft door an aircraft fitted with such a door
a technology for aircraft doors and aircraft, applied in the direction of aircraft ejection means, fuselages, launching weapons, etc., can solve the problems of increased volume, loss of space, and inability to use the mechanism normally providing the opening of doors
- Summary
- Abstract
- Description
- Claims
- Application Information
AI Technical Summary
Benefits of technology
Problems solved by technology
Method used
Image
Examples
first embodiment
[0055] In a first embodiment, shown in horizontal cross-section in FIG. 3, the intermediate bulkhead 18 is an integral part of a rigid structure 40 embodying the part of the door facing the interior of the aircraft. On the other hand, the frame 19 is added onto this structure 40 and has no specific rigidity.
[0056] Furthermore, in this embodiment in FIG. 3, tightness between the pressurised cabin and the outside of the aircraft is provided by a seal 42 placed around the door, approximately in the extension of the intermediate bulkhead 18. The housing 14 in which the slide is received is then not pressurised.
second embodiment
[0057] In the invention shown in FIG. 4, the intermediate bulkhead 18 and the frame 19 form an integral part of the rigid structure 40 of the door 10. In this case, the seal 42 placed around the door 10 is located approximately in the extension of the cover 16 forming the outer wall of the door 10. The housing 14 in which the slide is received is then located in the pressurised zone of the aircraft.
[0058] In a third embodiment of the invention shown diagrammatically in FIG. 5, the door structure is similar to that in the embodiment shown in FIG. 3 and the seal is arranged in the same way as in the second embodiment described with reference to FIG. 4.
[0059] More exactly, the back bulkhead 18 forms an integral part of the rigid structure 40 of the door 10, whereas the frame 19 is added onto this rigid structure.
[0060] On the other hand, the seal 42 is placed around the door 10 approximately in the extension of the cover 16 forming its outer wall.
fourth embodiment
[0061] A description will now be given of the invention with reference to FIGS. 6 to 8. To simplify matters, the corresponding components are denoted by the same numerical references.
[0062] In this case, the housing 14 is formed in the bottom part of the rigid structure of the door 10, within a bulge 13 which projects into the passenger cabin, as on existing doors. However, according to the invention, this housing 14 is delimited by a cover 16 on the outer face of the door.
[0063] The cover 16 is normally made integral with the rigid structure by fixing means (not shown) able to allow rapid opening of the cover when the slide stored in the folded away state in the housing 14 is to be deployed to provide an emergency evacuation from the aircraft. These fixing means may be of the same type as those which attach the cover 16 to the rigid door structure in the embodiments described previously with reference to FIGS. 1 to 5.
[0064] Moreover, setting de-setting means 45 are provided between...
PUM
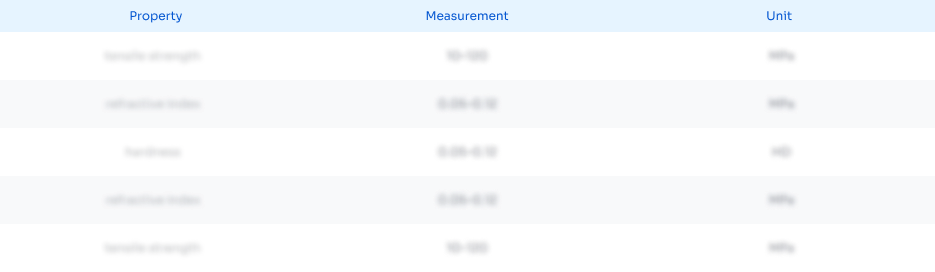
Abstract
Description
Claims
Application Information

- R&D
- Intellectual Property
- Life Sciences
- Materials
- Tech Scout
- Unparalleled Data Quality
- Higher Quality Content
- 60% Fewer Hallucinations
Browse by: Latest US Patents, China's latest patents, Technical Efficacy Thesaurus, Application Domain, Technology Topic, Popular Technical Reports.
© 2025 PatSnap. All rights reserved.Legal|Privacy policy|Modern Slavery Act Transparency Statement|Sitemap|About US| Contact US: help@patsnap.com