Supply of air to an air-conditioning circuit of an aircraft cabin
a technology of air conditioning circuit and aircraft cabin, which is applied in the direction of machines/engines, energy-saving board measures, and efficient propulsion technologies, etc., to achieve the effect of limiting the bleed air flow and significant and uncontrolled fuel consumption
- Summary
- Abstract
- Description
- Claims
- Application Information
AI Technical Summary
Benefits of technology
Problems solved by technology
Method used
Image
Examples
Embodiment Construction
[0043]FIG. 1 shows an aircraft turboprop engine 10, which herein is of the twin-spool type and comprises a low-pressure body 12 and a high-pressure body 14. The low-pressure body 12 drives a thrust propeller by means of a gearbox 16 or reduction gearbox, commonly referred to as PGB (Power Gear Box). Only the shaft 18 of the thrust propeller is shown in FIG. 1.
[0044]The low-pressure body 12 herein comprises only a turbine rotor connected by a shaft to the gearbox 16. The high-pressure body 14 comprises a compressor rotor connected by a shaft to a turbine rotor. The shaft of the high-pressure body 14, referred to as HP shaft, is tubular, and the shaft of the low-pressure body 12, referred to as LP shaft or power shaft, passes coaxially through said HP shaft. The LP shaft comprises a gear (not shown) at one end that is coupled to the shaft 18 of the thrust propeller by means of a series of gears of the gearbox 16.
[0045]The turboprop engine 10 comprises a gearbox 24 (referred to as AGB ...
PUM
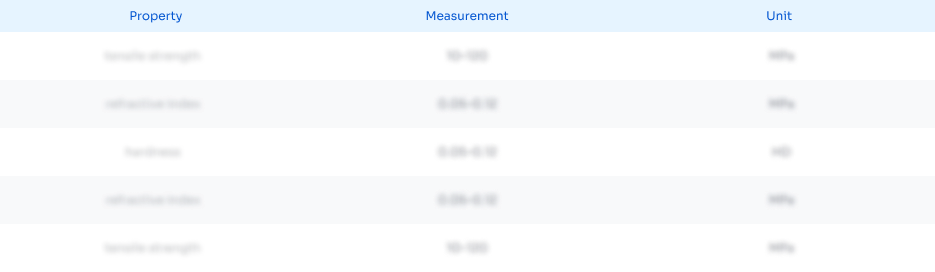
Abstract
Description
Claims
Application Information

- R&D
- Intellectual Property
- Life Sciences
- Materials
- Tech Scout
- Unparalleled Data Quality
- Higher Quality Content
- 60% Fewer Hallucinations
Browse by: Latest US Patents, China's latest patents, Technical Efficacy Thesaurus, Application Domain, Technology Topic, Popular Technical Reports.
© 2025 PatSnap. All rights reserved.Legal|Privacy policy|Modern Slavery Act Transparency Statement|Sitemap|About US| Contact US: help@patsnap.com