Negative valence jump dynamic torsion corrector
A technology of dynamic torque and calibration device, applied in the direction of measurement device, force/torque/work measuring instrument calibration/test, instrument, etc. Accurate and timely reflection of dynamic torque peak size, low numerical confidence and other issues, to achieve good economy, improved reliability and operability, and simple operation.
- Summary
- Abstract
- Description
- Claims
- Application Information
AI Technical Summary
Problems solved by technology
Method used
Image
Examples
Embodiment Construction
[0012] Referring to Fig. 1, the negative step dynamic torque calibration device includes a frame 1, a torque pier 2, a three-dimensional workbench 3, a test piece 4, a negative step dynamic torque generator 5 and a torque wall 6, and each component is arranged on on rack 1.
[0013] The frame 1 is a metal component, and is provided with a support frame corresponding to each composition. A guide rail for the torque wall 6 to move is laid on the upper surface of the torque wall 6; The guide rails on which the torque generator 6 moves and the corresponding lifting settings.
[0014] The torque pier 2 is a component for installing the test piece, and its structure is equipped with flanges on four sides to adapt to the dynamic characteristics of different test pieces, so that the calibration device has good versatility.
[0015] The three-dimensional workbench 3 supports a tray 33 by the shaft extension 32 of an adjustable worm gear box 31, and the tray 33 is provided with a suppo...
PUM
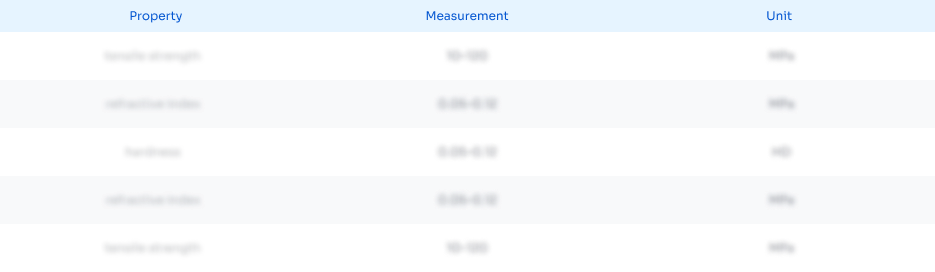
Abstract
Description
Claims
Application Information

- Generate Ideas
- Intellectual Property
- Life Sciences
- Materials
- Tech Scout
- Unparalleled Data Quality
- Higher Quality Content
- 60% Fewer Hallucinations
Browse by: Latest US Patents, China's latest patents, Technical Efficacy Thesaurus, Application Domain, Technology Topic, Popular Technical Reports.
© 2025 PatSnap. All rights reserved.Legal|Privacy policy|Modern Slavery Act Transparency Statement|Sitemap|About US| Contact US: help@patsnap.com