Calcium carbide dregs concrete pedestrian path brick and its preparing method
A technology of calcium carbide slag and concrete, which is applied to roads, roads, pavements paved with prefabricated blocks, etc., can solve the problems of easy cracks on the surface, heavy brick weight, and discarding, so as to improve product quality and later strength. , the effect of improving ease of handling
- Summary
- Abstract
- Description
- Claims
- Application Information
AI Technical Summary
Problems solved by technology
Method used
Image
Examples
specific Embodiment approach 1
[0016] Specific implementation method 1: This embodiment is composed of base material lower layer 1 and fabric upper layer 2, the upper layer and the lower layer are firmly combined as one, and the upper layer 2 of fabric is composed of 35-45 parts of colored cement and 55-65 parts of medium sand in parts by weight Composition, the base material lower layer 1 is composed of 5-15 parts of calcium carbide slag, 15-25 parts of cement, 15-20 parts of medium sand, 30-40 parts of crushed stone and 15-20 parts of mineral powder in parts by weight.
specific Embodiment approach 2
[0017] Specific embodiment two: The difference between this embodiment and specific embodiment one is that the upper layer 2 of the fabric is composed of 35 parts by weight of colored cement and 65 parts of medium sand, and the lower layer 1 of the base material is composed of 10 parts by weight of calcium carbide slag, It consists of 25 parts of cement, 15 parts of medium sand, 30 parts of gravel and 20 parts of mineral powder.
specific Embodiment approach 3
[0018] Specific embodiment three: the difference between this embodiment and specific embodiment one is that the upper layer 2 of the fabric is composed of 40 parts of colored cement and 60 parts of medium sand in parts by weight, and the lower layer 1 of the base material is composed of 5 parts of calcium carbide slag, It consists of 20 parts of cement, 20 parts of medium sand, 40 parts of gravel and 15 parts of mineral powder.
PUM
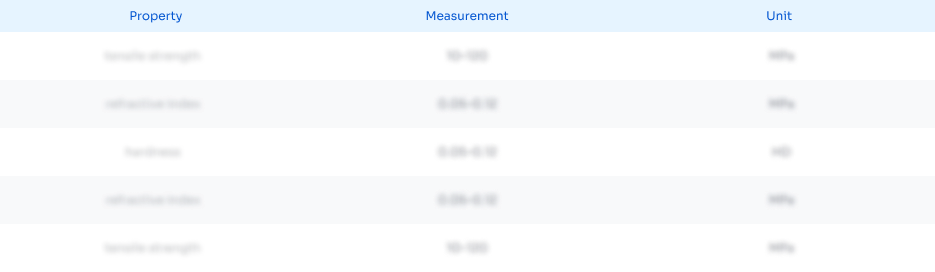
Abstract
Description
Claims
Application Information

- R&D
- Intellectual Property
- Life Sciences
- Materials
- Tech Scout
- Unparalleled Data Quality
- Higher Quality Content
- 60% Fewer Hallucinations
Browse by: Latest US Patents, China's latest patents, Technical Efficacy Thesaurus, Application Domain, Technology Topic, Popular Technical Reports.
© 2025 PatSnap. All rights reserved.Legal|Privacy policy|Modern Slavery Act Transparency Statement|Sitemap|About US| Contact US: help@patsnap.com