Magnet sensor arrangement
A technology of magnetic sensors and sensor elements, applied in the direction of converting sensor output, measuring devices, and adopting electrical devices, etc., which can solve problems such as eliminating deviations
- Summary
- Abstract
- Description
- Claims
- Application Information
AI Technical Summary
Problems solved by technology
Method used
Image
Examples
Embodiment Construction
[0031] FIG. 1 shows a schematic illustration of a magnetic sensor device 1 with a permanent magnet embodied as a split magnet 2 . The open magnet 2 has regions 4 and 5 magnetized in the same direction on both sides of the opening 3 , whose corresponding magnetic field B with the field lines depicted here is aligned in the direction of the sensor 6 . The sensor 6 is here embodied as an XMR sensor and has two magnetoresistive sensor elements 7 and 8 . The sensor elements 7 and 8 are shown positioned in the gradiometer arrangement at a gradiometer interval GM and detect changes in the respective field gradients, for example by a metallic transmitter element guided past the magnetic sensor arrangement 1 , for example FIG. 5 caused by the gear shown in .
[0032] The setting of the optimum operating point of the sensor 6 is achieved by the mutual spacing of the individual magnets 4 and 5 defined by the opening width sa and the opening depth st and can be matched to the gradiometer...
PUM
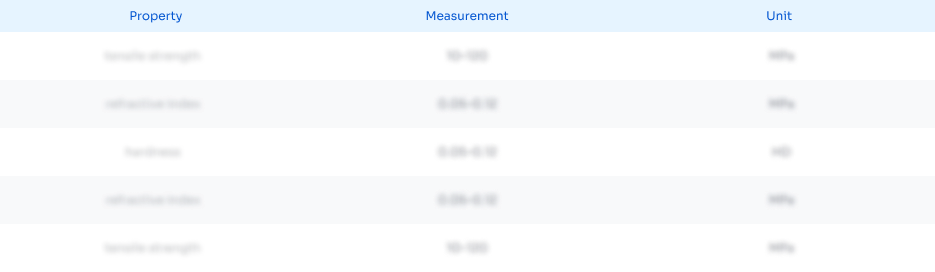
Abstract
Description
Claims
Application Information

- R&D
- Intellectual Property
- Life Sciences
- Materials
- Tech Scout
- Unparalleled Data Quality
- Higher Quality Content
- 60% Fewer Hallucinations
Browse by: Latest US Patents, China's latest patents, Technical Efficacy Thesaurus, Application Domain, Technology Topic, Popular Technical Reports.
© 2025 PatSnap. All rights reserved.Legal|Privacy policy|Modern Slavery Act Transparency Statement|Sitemap|About US| Contact US: help@patsnap.com