Method for quantitatively identifying rolling bearing damage
A rolling bearing, quantitative identification technology, applied in the direction of measuring devices, special data processing applications, instruments, etc., can solve the problems that are not suitable for identifying early damage faults of rolling bearings, and it is difficult to fully extract fault information features
- Summary
- Abstract
- Description
- Claims
- Application Information
AI Technical Summary
Problems solved by technology
Method used
Image
Examples
Embodiment 1
[0123] Construct the impulse response simulation signal x(t) of two carrier centers of a modulation source to simulate the response signal of a rolling bearing with an outer ring fault and multiple carrier centers:
[0124] x ( t ) = Σ i = 1 42 ( e - ζ 2 πf 1 ( t - i / f ou ) sin 2 πf 1 ( t - i / ...
Embodiment 2
[0131] In order to verify the correctness of the method described in this paper, early damage faults of the outer ring of rolling bearings were set up on the rolling bearing test bench. The model of the rolling bearing is 552732QT, and its parameters are as follows: the inner diameter is 160mm, the outer diameter is 290mm, the roller diameter is 34mm, and the number of rollers is 17. During the test, the shaft rotation frequency of the test bench is 515r / min.
[0132] The sampling frequency is set to 12800Hz, the number of sampling points is 8192, Figure 5 (a) is the rolling bearing vibration signal collected from the rolling bearing test bench, the rolling bearing vibration signal is subjected to Hilbert envelope demodulation, and the decibel value of the envelope spectrum is obtained as Figure 5 (b) shown.
[0133] The rolling bearing vibration signal is decomposed and reconstructed by three layers of second-generation wavelet packets, and the reconstructed signals of ei...
PUM
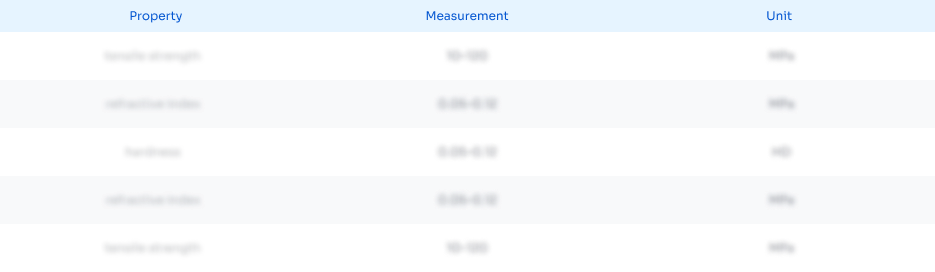
Abstract
Description
Claims
Application Information

- R&D
- Intellectual Property
- Life Sciences
- Materials
- Tech Scout
- Unparalleled Data Quality
- Higher Quality Content
- 60% Fewer Hallucinations
Browse by: Latest US Patents, China's latest patents, Technical Efficacy Thesaurus, Application Domain, Technology Topic, Popular Technical Reports.
© 2025 PatSnap. All rights reserved.Legal|Privacy policy|Modern Slavery Act Transparency Statement|Sitemap|About US| Contact US: help@patsnap.com