Solvent recovery method for cellulose fiber preparation with ion liquid as solvent
A technology of cellulose fibers and ionic liquids, which is applied in the fields of rayon recycling, fiber chemical characteristics, and final product manufacturing, can solve the problems of complex synthesis and purification processes and high production costs, and achieve environmental protection and reduce production costs. Effect of saving resources and energy
- Summary
- Abstract
- Description
- Claims
- Application Information
AI Technical Summary
Problems solved by technology
Method used
Examples
example 1
[0021] With [BMIM]Cl and [BMIM]BF 4 The molar ratio is 8: 2 ionic liquid mixed solution as solvent, the spinning solution solution of preparation wood pulp 8% carries out wet spinning, uses 20% mixed solution-water solution as coagulant, after spinning for a period of time, take out 1000g Coagulation bath, learn after chemical titration that this 1000g mixed solution contains about 277.6g of ionic liquid mixed solution.
[0022] Add 2000g of water to 1000g of the mixture, stir well.
[0023] Use a 0.22 μm microporous membrane to filter under reduced pressure.
[0024] Under the condition of 150 Pa, distilled under reduced pressure at 95° C. for 2 hours, then distilled under normal pressure at 120° C. for 2 hours, finally obtained about 270.4 g of the ionic liquid mixture, with a recovery rate of 97.41%.
example 2
[0026] With [BMIM]Cl and [BMIM]BF 4 The ionic liquid mixed solution with a molar ratio of 7:3 is used as a solvent to prepare a 7% spinning solution of bamboo pulp for wet spinning, and 18% mixed solution-water solution is used as a coagulant. After spinning for a period of time, 1000g of bamboo pulp is taken out Coagulation bath, learn after chemical titration that this 1000g mixed solution contains about 203.5g of ionic liquid mixed solution.
[0027] Add 2000g of water to 1000g of the mixture, stir well.
[0028] Use a 0.22 μm microporous membrane to filter under reduced pressure.
[0029] Under the condition of 150 Pa, distilled under reduced pressure at 95° C. for 2 hours, then distilled under normal pressure at 120° C. for 2 hours, finally obtained about 200.1 g of the ionic liquid mixture, with a recovery rate of 98.33%.
[0030] Tests have proved that the recovered ionic liquid mixture has high purity and can be recycled, so this recovery method has high use value.
PUM
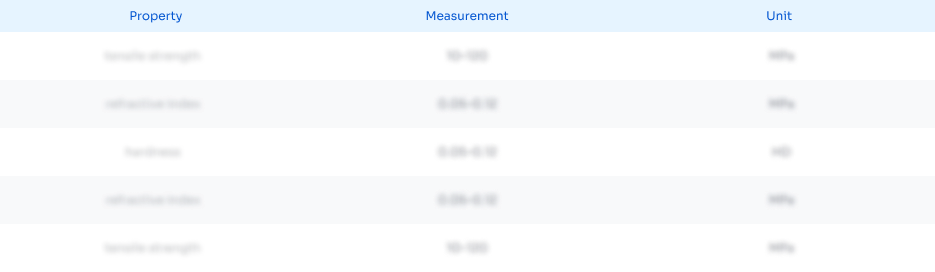
Abstract
Description
Claims
Application Information

- R&D
- Intellectual Property
- Life Sciences
- Materials
- Tech Scout
- Unparalleled Data Quality
- Higher Quality Content
- 60% Fewer Hallucinations
Browse by: Latest US Patents, China's latest patents, Technical Efficacy Thesaurus, Application Domain, Technology Topic, Popular Technical Reports.
© 2025 PatSnap. All rights reserved.Legal|Privacy policy|Modern Slavery Act Transparency Statement|Sitemap|About US| Contact US: help@patsnap.com