Inserting strip sewing machine
A sewing machine and molding technology, which is applied to sewing machine components, sewing equipment, cloth feeding mechanism, etc., can solve the problems of bulky and inconvenient cloth feeding mechanism with large presser feet, and achieve the effect of improving workability and reducing the number of parts
- Summary
- Abstract
- Description
- Claims
- Application Information
AI Technical Summary
Problems solved by technology
Method used
Image
Examples
Embodiment Construction
[0024] (Overall configuration of the embodiment of the present invention)
[0025] Below, based on Figure 1 to Figure 5 , an embodiment of the present invention, that is, a panel sewing machine 10 will be described. figure 1 as well as figure 2 It is a perspective view showing the overall schematic configuration of the panel sewing machine 10 . And in this embodiment, each direction is determined on the basis of the XYZ axes shown in each figure, the Z-axis direction is consistent with the up-and-down movement direction of the movable cutter 42 described later, and the plane on which the sewing operation is performed is consistent with The Z-axis direction is vertical, the direction of cloth feeding parallel to the working plane is defined as the X-axis direction, and the direction perpendicular to the X-axis direction parallel to the working plane is defined as the Y-axis direction.
[0026] image 3 It is an explanatory diagram showing the arrangement relationship of t...
PUM
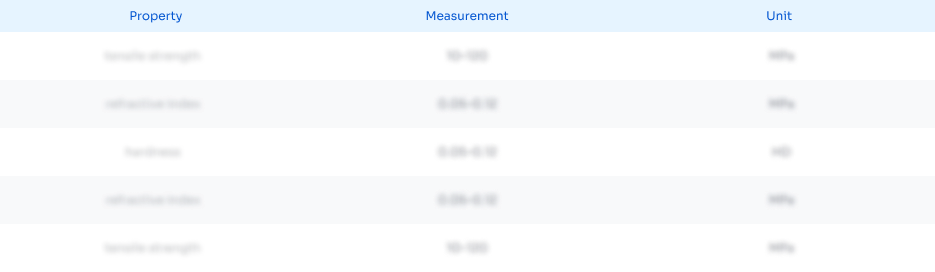
Abstract
Description
Claims
Application Information

- R&D
- Intellectual Property
- Life Sciences
- Materials
- Tech Scout
- Unparalleled Data Quality
- Higher Quality Content
- 60% Fewer Hallucinations
Browse by: Latest US Patents, China's latest patents, Technical Efficacy Thesaurus, Application Domain, Technology Topic, Popular Technical Reports.
© 2025 PatSnap. All rights reserved.Legal|Privacy policy|Modern Slavery Act Transparency Statement|Sitemap|About US| Contact US: help@patsnap.com