Needle valve nozzle
A needle valve and nozzle port technology, applied in the field of needle valve nozzles, can solve the problems of flush closure of nozzle ports, unclean riser points, complex structure, etc., and achieve high service life, simple geometry, and reliable guidance. Effect
- Summary
- Abstract
- Description
- Claims
- Application Information
AI Technical Summary
Problems solved by technology
Method used
Image
Examples
Embodiment Construction
[0024] figure 1 The needle valve orifice designated as a whole by 10 is a component part of the (not shown) die-casting tool. It has a preferably externally heated nozzle body 20 , in which a (not visible) material tube is formed, which delimits a melt channel 30 concentrically to the longitudinal axis L of the needle valve nozzle 10 . A nozzle mouthpiece 40 of a highly thermally conductive material is preferably screwed from below into the nozzle body 20 , and the melt channel 30 extends cylindrically downwards without a change in cross-section.
[0025] The melt to be processed, eg metal, silicon or plastic melt, is conveyed via the melt channel 30 into a mold cavity (not shown in detail). The cavity is formed between at least two mold parts 50 which are fastened to the formwork (not shown) and delimit a riser 51 concentrically to the longitudinal axis L of the heating channel nozzle 10 .
[0026] Between the nozzle mouth piece 40 and the mold part 50, a centering body 80 ...
PUM
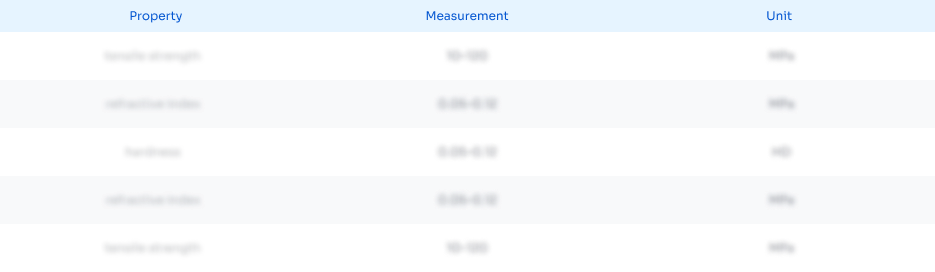
Abstract
Description
Claims
Application Information

- Generate Ideas
- Intellectual Property
- Life Sciences
- Materials
- Tech Scout
- Unparalleled Data Quality
- Higher Quality Content
- 60% Fewer Hallucinations
Browse by: Latest US Patents, China's latest patents, Technical Efficacy Thesaurus, Application Domain, Technology Topic, Popular Technical Reports.
© 2025 PatSnap. All rights reserved.Legal|Privacy policy|Modern Slavery Act Transparency Statement|Sitemap|About US| Contact US: help@patsnap.com