Glass fiber impregnating resin wound-type composite insulator core and preparing method
A composite insulator and glass fiber technology, applied in the direction of insulators, suspension/strain insulators, electrical components, etc., can solve the problems of high tensile strength and poor bending strength of the mandrel, achieve low production costs, reduce the effective distance to the ground, Effect of Reliability Improvement
- Summary
- Abstract
- Description
- Claims
- Application Information
AI Technical Summary
Problems solved by technology
Method used
Image
Examples
Embodiment 1
[0030] 1. Take the resin-based impregnating composition by weight ratio, and the weight ratio of the composition is: epoxy resin: methyltetrahydrophthalic anhydride: S-440=90:85:1
[0031] ②. Melt the resin-based impregnating composition at a temperature of 20°C, and fully stir it at a speed of 150 rpm, and the resin base must not contain air bubbles;
[0032] ③. Put one end of the yarn splint fixed on the CNC winding machine through the resin-based glue tank to put the glass fiber epoxy winding yarn monofilament 3 into the melted resin-based solution, and then fix one end of the monofilament 3 to the metal ring 2 superior;
[0033] ④. Use the CNC winding machine to determine the center distance of the upper and lower metal rings and the diameter of the wound composite insulator mandrel 1 according to the customer's requirements for voltage level and tensile force. After programming the technical parameters, enter the CNC programming machine, and insulator core according to th...
Embodiment 2
[0035] 1. Take the resin-based impregnating composition by weight ratio, and the weight ratio of the composition is: epoxy resin: methyltetrahydrophthalic anhydride: S-440=95:90:1,
[0036] ②. Melt the resin base at a temperature of 25° C. and fully stir it evenly. The resin base must not contain air bubbles; other steps are the same as in Example 1
Embodiment 3
[0038] 1. Take the resin-based impregnating composition by weight ratio, and the weight ratio of the composition is: epoxy resin: methyltetrahydrophthalic anhydride: S-440=100:80:1,
[0039] ②. Melt the resin base at a temperature of 30°C and fully stir it evenly. The resin base must not contain air bubbles; other steps are the same as in Example 1
PUM
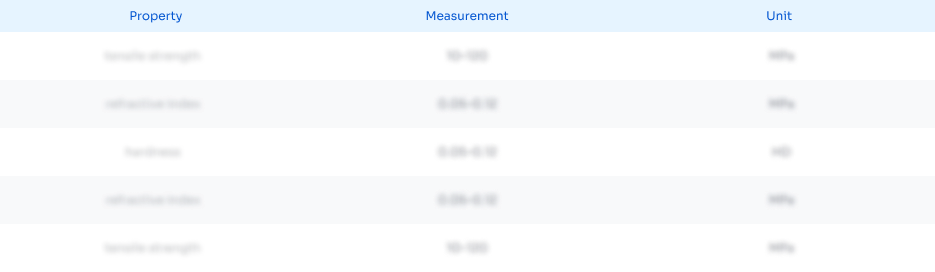
Abstract
Description
Claims
Application Information

- R&D
- Intellectual Property
- Life Sciences
- Materials
- Tech Scout
- Unparalleled Data Quality
- Higher Quality Content
- 60% Fewer Hallucinations
Browse by: Latest US Patents, China's latest patents, Technical Efficacy Thesaurus, Application Domain, Technology Topic, Popular Technical Reports.
© 2025 PatSnap. All rights reserved.Legal|Privacy policy|Modern Slavery Act Transparency Statement|Sitemap|About US| Contact US: help@patsnap.com