Method for extracting ultrathin starch from overflow materials produced in the process of preparing wheat starch
A production process, wheat starch technology, applied in the field of material extraction of superfine starch, can solve the problems of increasing fixed costs, low conversion rate of powdered sugar, etc., and achieve the effect of increasing yield
- Summary
- Abstract
- Description
- Claims
- Application Information
AI Technical Summary
Problems solved by technology
Method used
Examples
Embodiment 1
[0024] (1) 993.6 tons of overflows with a solid content of 3.1% were generated during the production process of receiving wheat starch. (2), utilize the high-speed centrifuge to concentrate the overflow to obtain 226.8 tons of material with a solid content of 10.2% (wherein the starch content is 71.2%), and the remaining materials (underflow) enter the starch production system as process water. (3), carry out SO2 absorption to the concentrate to pH 3.2. (4) At this time, the temperature of the material was 38° C., adding cellulose composite enzyme with a solid weight of 0.5‰ in the overflow after concentration, and stirring for 2 hours. (5) After centrifugal separation and cleaning of the reacted material, 21.5 tons of wet material with a solid content of 63.9% was obtained. (6) 15.8 tons of superfine starch are obtained after the wet material obtained after separation is air-dried. After product inspection, the moisture content is 13.2%, the protein content is 0.65%, the yi...
Embodiment 2
[0026] (1) 993.6 tons of overflows with a solid content of 3.1% were generated during the production process of receiving wheat starch. (2), utilize the high-speed centrifuge to concentrate the overflow to obtain 226.8 tons of material with a solid content of 12% (wherein the starch content is 79.4%), and the remaining materials (underflow) enter the starch production system as process water. (3), carry out SO2 absorption to the concentrate to pH 3.0. (4) At this time, the temperature of the material is 35° C., adding a cellulose composite enzyme with a solid weight of 0.8‰ in the overflow after concentration, and stirring for 1 hour. (5) After centrifugal separation and cleaning of the reacted material, 18.4 tons of wet material with a solid content of 65.2% was obtained. (6) The wet material obtained after separation is air-dried to obtain 13.8 tons of superfine starch. After product inspection, the moisture content is 13.2%, the protein content is 0.65%, the yield of pure...
Embodiment 3
[0028] (1) 993.6 tons of overflows with a solid content of 3.1% were generated during the production process of receiving wheat starch. (2), utilize the high-speed centrifuge to condense the overflow to obtain 117.8 tons of materials with a solid content of 15% (wherein the starch content is 71.2%), and the remaining materials (top flow) enter the starch production system as process water. (3), carry out SO2 absorption to the concentrate to pH 3.5. (4) At this time, the temperature of the material was 55° C., adding cellulose composite enzyme with a solid weight of 1‰ in the overflow after concentration, and stirring for 3 hours. (5) After centrifugal separation and cleaning of the reacted material, 19.1 tons of wet material with a solid content of 64.8% was obtained. (6) 14.3 tons of ultra-fine starch were obtained after the wet material obtained after separation was air-dried. After product inspection, the moisture content is 13.2%, the protein content is 0.65%, the yield ...
PUM
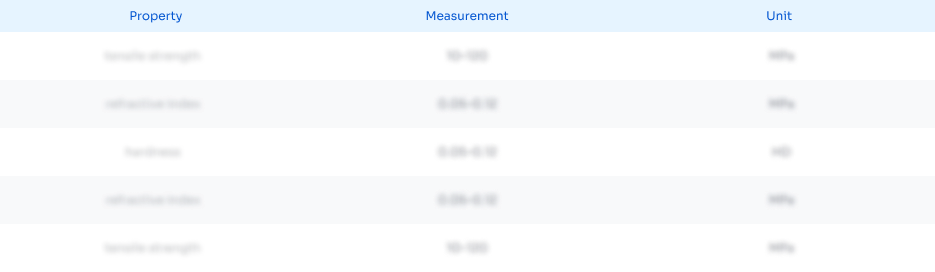
Abstract
Description
Claims
Application Information

- R&D
- Intellectual Property
- Life Sciences
- Materials
- Tech Scout
- Unparalleled Data Quality
- Higher Quality Content
- 60% Fewer Hallucinations
Browse by: Latest US Patents, China's latest patents, Technical Efficacy Thesaurus, Application Domain, Technology Topic, Popular Technical Reports.
© 2025 PatSnap. All rights reserved.Legal|Privacy policy|Modern Slavery Act Transparency Statement|Sitemap|About US| Contact US: help@patsnap.com