Path control system used for hydraulic digger operating device and its method
A technology for hydraulic excavators and working devices, which is applied in control/adjustment systems, position/direction control, non-electric variable control and other directions, can solve the problems of difficulty in setting parameters, PID parameters are not easy to set, and control effects cannot be obtained. The effect of work cycle, improving work efficiency and work quality
- Summary
- Abstract
- Description
- Claims
- Application Information
AI Technical Summary
Problems solved by technology
Method used
Image
Examples
Embodiment Construction
[0040] The control system of the present invention includes boom hydraulic cylinder 208, arm hydraulic cylinder 209, bucket hydraulic cylinder 210, main control valve 207, electromagnetic proportional pilot valve 205, gear pump 211, overflow valve 206, oil filter 212, Boom 104, stick 106, bucket 108, wherein:
[0041] 1. A boom angle detection mechanism 103 and a stick angle detection mechanism 105 are respectively provided at the hinge joints of the boom 104 and the working device 102 , the hinge joints of the boom 104 and the stick 106 , and the joints of the stick 106 and the bucket 108 , bucket angle detection mechanism 107;
[0042] 2. It has a DSP controller 201, which is used to receive the angle signals measured by the boom angle detection mechanism 103, the arm angle detection mechanism 105, and the bucket angle detection mechanism 107 sent through A / D data conversion, and the boom hydraulic cylinder 208 pressure, arm hydraulic cylinder 209 pressure, bucket hydraulic...
PUM
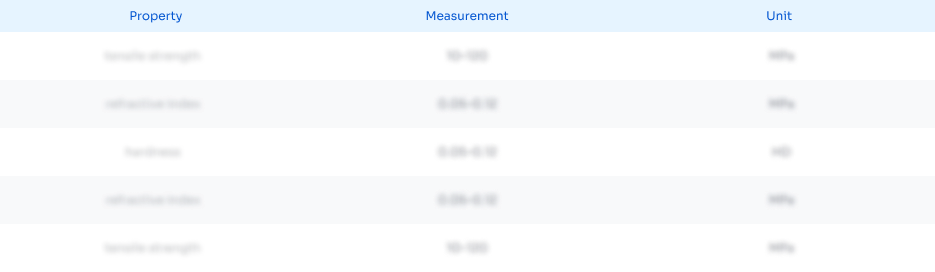
Abstract
Description
Claims
Application Information

- R&D
- Intellectual Property
- Life Sciences
- Materials
- Tech Scout
- Unparalleled Data Quality
- Higher Quality Content
- 60% Fewer Hallucinations
Browse by: Latest US Patents, China's latest patents, Technical Efficacy Thesaurus, Application Domain, Technology Topic, Popular Technical Reports.
© 2025 PatSnap. All rights reserved.Legal|Privacy policy|Modern Slavery Act Transparency Statement|Sitemap|About US| Contact US: help@patsnap.com