Pieparation method for fabricating raw bamboo into spinnable bamboo fibers
A production method and technology of bamboo fiber, applied in the direction of chemical post-treatment of fiber, fiber treatment, plant raw materials, etc., can solve the problems of long process time, low yarn forming strength, high difficulty, etc., and achieve strong operability and spinnability Strong and soft effect
- Summary
- Abstract
- Description
- Claims
- Application Information
AI Technical Summary
Problems solved by technology
Method used
Examples
Embodiment 1
[0011] Use ordinary moso bamboo as raw material, and make bamboo fiber according to the following process:
[0012] 1. The original bamboo is cut to length according to the length of the bamboo joints through shaping;
[0013] 2. Place the cut bamboo joints in a pressure vessel, use superheated steam of 1-2Mpa, steam for 1 hour per kilogram of bamboo joints, and steam for 1 hour to remove lignin and pectin in the original bamboo Other impurities:
[0014] 3. Soak the cooked bamboo joints with a 5% aqueous solution containing straw enzyme bacteria (produced according to conventional methods) and bamboo joints for 2 hours, then heat the aqueous solution containing straw enzyme bacteria and bamboo joints to 80 degrees, and then soak In 2 hours, the lignin and pectin residues in the bamboo joints and the sugar and fat in the bamboo joints are swallowed by the straw enzyme bacteria, so that the bamboo joints are further desugared, degreased and softened, and become thick fibrous b...
Embodiment 2
[0022] Use ordinary mangosteen as raw material, and make bamboo fiber according to the following process:
[0023] 1. The original bamboo is cut to length according to the length of the bamboo joints through shaping;
[0024] 2. Place the cut bamboo joints in a pressure vessel, use superheated steam of 1-2Mpa, steam for 3 hours per kilogram of bamboo joints, and steam for 3 hours to remove lignin and pectin in the original bamboo other impurities;
[0025] 3. The bamboo joints after cooking are soaked together with the bamboo joints with 10% aqueous solution containing straw enzyme bacteria (made by conventional method) for 6 hours, then heated to 90 degrees with the aqueous solution containing straw enzyme bacteria and bamboo joints, and then soaked for 3 Hours, the lignin and pectin residues in the bamboo joints and the sugar and fat in the bamboo joints are swallowed by the straw enzyme bacteria, so that the bamboo joints are further desugared, degreased and softened, and ...
Embodiment 3
[0033] Use ordinary emerald bamboo as raw material, and make bamboo fiber according to the following process:
[0034] 1. The original bamboo is cut to length according to the length of the bamboo joints through shaping;
[0035] 2. Place the cut bamboo joints in a pressure vessel, use superheated steam of 1-2Mpa, and steam for 3 hours to remove lignin and pectin in the original bamboo, according to the steam supply of 2 cubic meters per kilogram of bamboo joints per hour other impurities;
[0036] 3. Soak the cooked bamboo joints with 10% aqueous solution containing straw enzyme bacteria (produced according to conventional methods) and bamboo joints for 5 hours, then heat the aqueous solution containing straw enzyme bacteria and bamboo joints to 80 degrees, and then soak In 2 hours, the lignin and pectin residues in the bamboo joints and the sugar and fat in the bamboo joints are swallowed by the straw enzyme bacteria, so that the bamboo joints are further desugared, degreas...
PUM
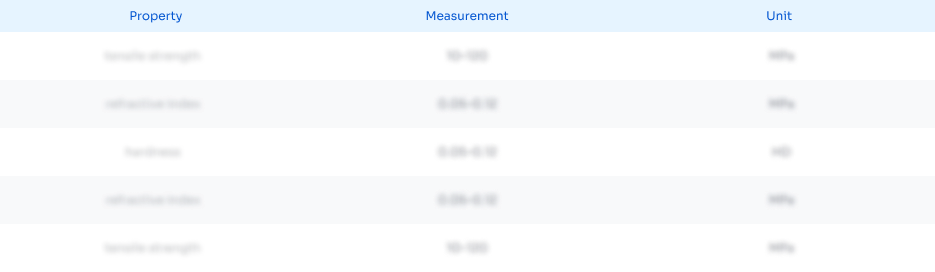
Abstract
Description
Claims
Application Information

- R&D
- Intellectual Property
- Life Sciences
- Materials
- Tech Scout
- Unparalleled Data Quality
- Higher Quality Content
- 60% Fewer Hallucinations
Browse by: Latest US Patents, China's latest patents, Technical Efficacy Thesaurus, Application Domain, Technology Topic, Popular Technical Reports.
© 2025 PatSnap. All rights reserved.Legal|Privacy policy|Modern Slavery Act Transparency Statement|Sitemap|About US| Contact US: help@patsnap.com