Method for producing a part with a coil and electric machine comprising such a part
A manufacturing method and coil technology, which is applied in the manufacture of motor generators, electrical components, electromechanical devices, etc., can solve the problem of low filling coefficient of coils, and achieve low material cost, high filling coefficient of winding wire, and small stop The effect of torque
- Summary
- Abstract
- Description
- Claims
- Application Information
AI Technical Summary
Problems solved by technology
Method used
Image
Examples
Embodiment Construction
[0018] Below, refer to figure 1 - Figure 5 to illustrate the method of manufacture of an electric machine with improved coil windings proposed by the invention.
[0019] figure 1 The stator 1 of the electric machine is shown, here the stator 1 has a surrounding ring 2 and a plurality of stator teeth 3 . Such as figure 2 As shown in detail, the stator teeth are T-shaped in cross-section and have tangentially extending projections 5 , 6 at their inwardly facing end 2 , also called tooth feet.
[0020] figure 2 A schematic sectional front view of the stator is shown, here a coil 9 is shown around the stator teeth 3 , which has a plurality of windings 10 made of at least one type of wire. To see it more clearly, in figure 2 - Only one coil is shown exactly in each case in FIG. 5 . The coil 9 is wound on the stator tooth 3 by a known method, for example. Such as figure 2 It is clearly shown that, due to the geometrical conditions and the winding method, some gaps 13 are...
PUM
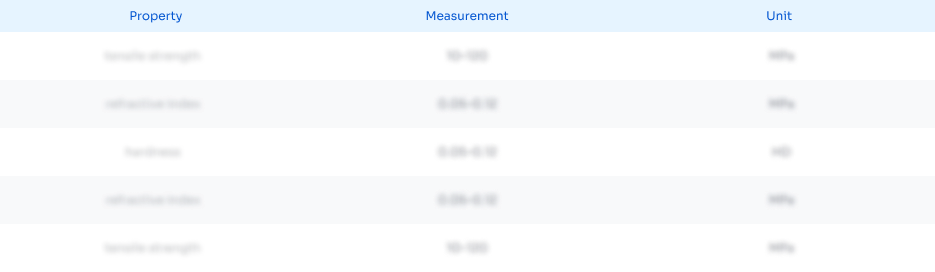
Abstract
Description
Claims
Application Information

- R&D
- Intellectual Property
- Life Sciences
- Materials
- Tech Scout
- Unparalleled Data Quality
- Higher Quality Content
- 60% Fewer Hallucinations
Browse by: Latest US Patents, China's latest patents, Technical Efficacy Thesaurus, Application Domain, Technology Topic, Popular Technical Reports.
© 2025 PatSnap. All rights reserved.Legal|Privacy policy|Modern Slavery Act Transparency Statement|Sitemap|About US| Contact US: help@patsnap.com