Transtion joint for reducing impacted vibration to rail joint by heavy load train
A transition joint, shock vibration technology
- Summary
- Abstract
- Description
- Claims
- Application Information
AI Technical Summary
Problems solved by technology
Method used
Image
Examples
Embodiment Construction
[0013] The present invention will be described in further detail below in conjunction with the accompanying drawings.
[0014] see Figure 1~3 , a transition joint for reducing impact vibration at rail joints of heavy-duty vehicles. The transition joint is divided into two parts: an outer joint 2 and an inner joint 4. The outer joint 2 and the inner joint 4 have connecting holes respectively, and are connected by bolts 3. There is an expansion joint 5 after the connection.
[0015] The connecting holes on the outer joint 2 and the inner joint 4 are waist-shaped holes.
[0016] The working principle of the present invention is, at the end of former steel rail 1, respectively weld the outer joint 2 of the present invention and the inner joint 4, then the inner joint and the outer joint are connected in the waist-shaped hole with bolts and get final product, (see Figure 4 ). When the wheel passes through the expansion joint at the joint, there is always some part to bear the ...
PUM
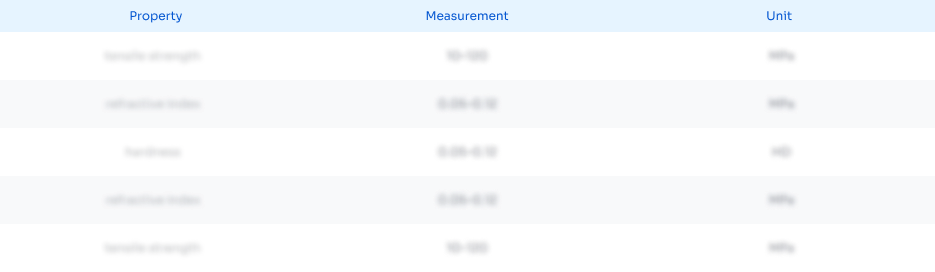
Abstract
Description
Claims
Application Information

- R&D
- Intellectual Property
- Life Sciences
- Materials
- Tech Scout
- Unparalleled Data Quality
- Higher Quality Content
- 60% Fewer Hallucinations
Browse by: Latest US Patents, China's latest patents, Technical Efficacy Thesaurus, Application Domain, Technology Topic, Popular Technical Reports.
© 2025 PatSnap. All rights reserved.Legal|Privacy policy|Modern Slavery Act Transparency Statement|Sitemap|About US| Contact US: help@patsnap.com