Method and device for extruding curved extrusion profiles
A technology of extruded profiles, extrusion methods, applied in the field of extrusion and installation of curved extruded profiles
- Summary
- Abstract
- Description
- Claims
- Application Information
AI Technical Summary
Problems solved by technology
Method used
Image
Examples
Embodiment Construction
[0022] The blank 2 to be extruded is supplied to an extrusion machine 1 as shown in FIG. 1 by means of a charging device 3 . The profile strip extruded through the forming extrusion die exits the front cross member 4 and, during linear extrusion, arrives on an exit roller table 6 arranged at the exit 5 of the extruder.
[0023] In this exemplary embodiment, however, rounded profile strips 7 a , 7 b are produced which, relative to the straight extrusion direction 8 , have a constant curvature towards one side. When bending the strip with a desired radius, wherein in FIG. 1 for example the profiled strip 7a or 7b is shown with two different radii, there is an arrow 9 between the front beam 4 and the delivery roller table 6 and Correspondingly, there is a guiding tool which acts on the web and which can cooperate with a further, not shown, upstream radius sensor.
[0024] On the side corresponding to the bending direction of the profiled strips 7a, 7b, a support frame or support...
PUM
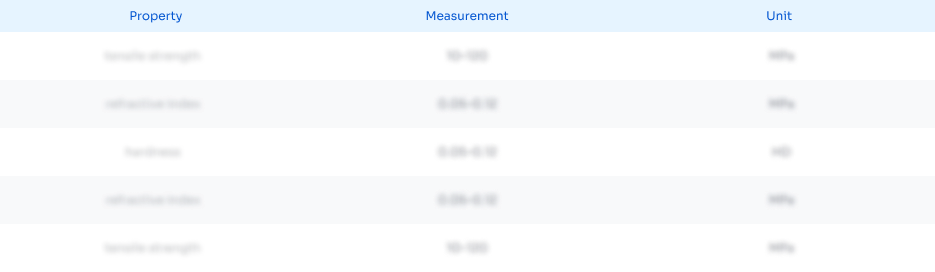
Abstract
Description
Claims
Application Information

- R&D
- Intellectual Property
- Life Sciences
- Materials
- Tech Scout
- Unparalleled Data Quality
- Higher Quality Content
- 60% Fewer Hallucinations
Browse by: Latest US Patents, China's latest patents, Technical Efficacy Thesaurus, Application Domain, Technology Topic, Popular Technical Reports.
© 2025 PatSnap. All rights reserved.Legal|Privacy policy|Modern Slavery Act Transparency Statement|Sitemap|About US| Contact US: help@patsnap.com