Preparation of low-resistance / high-resistance composite film through ultrasonic spray pyrolysis
A technology of ultrasonic spray pyrolysis and composite thin film, which is applied in the field of new optoelectronic materials and can solve the problems of small deposition area, high investment and low deposition rate
- Summary
- Abstract
- Description
- Claims
- Application Information
AI Technical Summary
Problems solved by technology
Method used
Image
Examples
Embodiment Construction
[0018] Embodiments of the present invention will be described in detail below in conjunction with the accompanying drawings.
[0019] The transparent conductive film is prepared by ultrasonic spray pyrolysis film forming technology.
[0020] First, the metal salt (such as SnCl 4 .5H 2 O) be contained in liquid, and liquid is deionized water, a small amount of hydrochloric acid, ethanol, then adds ammonium fluoride and hydrofluoric acid. The deposition temperature is 340-520° C., and the deposition rate is approximately 10-300 nm / sec. By adjusting the deposition temperature, flow rate of carrying gas, fluorine content, tin salt concentration and deposition time, transparent SnO with a sheet resistance of 4.7Ω can be deposited. 2 conductive film. The metal tin salt is changed to metal zinc salt, and aluminum chloride is added to the reaction liquid to deposit ZnO:Al transparent conductive film. Similarly, this method can be used to prepare CdO, ITO, CdSnO 4 and Zn 2 SnO ...
PUM
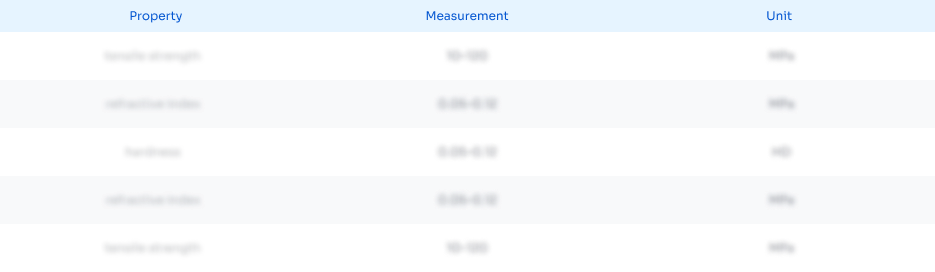
Abstract
Description
Claims
Application Information

- Generate Ideas
- Intellectual Property
- Life Sciences
- Materials
- Tech Scout
- Unparalleled Data Quality
- Higher Quality Content
- 60% Fewer Hallucinations
Browse by: Latest US Patents, China's latest patents, Technical Efficacy Thesaurus, Application Domain, Technology Topic, Popular Technical Reports.
© 2025 PatSnap. All rights reserved.Legal|Privacy policy|Modern Slavery Act Transparency Statement|Sitemap|About US| Contact US: help@patsnap.com