Multiple optical axises photoelectric sensor
A photoelectric sensor, multi-optical axis technology, applied in the direction of instruments, circuits, electric switches, etc., to achieve the effect of preventing adverse situations
- Summary
- Abstract
- Description
- Claims
- Application Information
AI Technical Summary
Problems solved by technology
Method used
Image
Examples
Embodiment 1
[0020] Embodiment 1 of the multi-optical axis photoelectric sensor of the present invention will be described below with reference to FIGS. 1 to 4 . As shown in Fig. 1 and Fig. 2, the multi-optical axis photoelectric sensor of this embodiment is installed in the vicinity of the press machine in the production line, between the dangerous area D where the operator is prohibited from entering and the safe area where the operator is allowed to enter. at the boundary between.
[0021] This multi-optical axis photoelectric sensor is configured in a state where a light projector 1 (light projecting unit) and a light receiver 2 (light receiving unit) face each other, and has, for example, 12 channels of optical axes. On the surface of the light projector 1 facing the light receiver 2, one (total 12) light projecting elements 11a to 11l arranged on each channel are arranged in a row in the vertical direction, and on the surface of the light receiver 2 facing the light projector 1 On t...
Embodiment 2
[0040] Embodiment 2 of the present invention will be described below with reference to FIG. 5 . Parts that are the same as those in the first embodiment are marked with the same symbols to omit repeated descriptions, and descriptions on the same functions and effects are also omitted.
[0041] In this embodiment, the transmissive photoelectric sensors 4A, 4B (corresponding to "external equipment", "external sensors") that detect the shading caused by the workpiece W are installed in front of the light receivers 2A and 2B (opposite to the danger zone D). The safe area side), the signal output lines of these photoelectric sensors 4 are connected to the input ports 27 of the respective photoreceivers 2A, 2B. In addition, when the light receivers 2A and 2B receive the detection signals from the corresponding photosensors 4A, 4B, the light receiving signals from the light receiving elements 11a to 11l constituting the channels stored in the memory 25A are invalidated for a predeterm...
Embodiment 3
[0047] Embodiment 3 of the present invention will be described below with reference to FIG. 6 to FIG. 9 . The same parts as in Embodiment 1 are marked with the same symbols to omit repeated descriptions, and the descriptions on the same functions and effects are also omitted.
[0048] In this embodiment, the workpieces W flow through the conveying lines (not shown in the figure) vertically stacked in three layers, and the corresponding workpieces W are sent into the dangerous area D respectively. The light projector 1 and the light receiver 2 are arranged in a group on both sides of the conveying line, and three sets of photosensors 4A to 4C are arranged at predetermined intervals in the longitudinal direction in front of it (on the side of the safe area opposite to the dangerous area D). The optical axis of the photoelectric sensor 4A on the top layer is located between the second and third channels of the light emitter 1 and the light receiver 2, the optical axis of the photo...
PUM
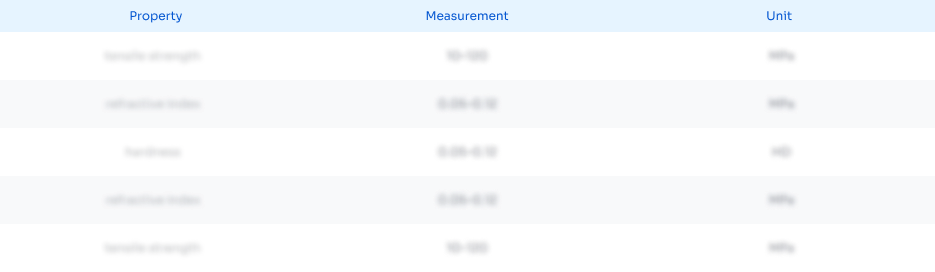
Abstract
Description
Claims
Application Information

- R&D
- Intellectual Property
- Life Sciences
- Materials
- Tech Scout
- Unparalleled Data Quality
- Higher Quality Content
- 60% Fewer Hallucinations
Browse by: Latest US Patents, China's latest patents, Technical Efficacy Thesaurus, Application Domain, Technology Topic, Popular Technical Reports.
© 2025 PatSnap. All rights reserved.Legal|Privacy policy|Modern Slavery Act Transparency Statement|Sitemap|About US| Contact US: help@patsnap.com