Catalytic cracking process of refining biological oil
A catalytic cracking, bio-oil technology, applied in the direction of biological raw materials, petroleum industry, preparation of liquid hydrocarbon mixtures, etc., can solve the problems of high viscosity, instability, poor volatility, etc.
- Summary
- Abstract
- Description
- Claims
- Application Information
AI Technical Summary
Problems solved by technology
Method used
Examples
Embodiment 1
[0016] The catalyst used in the experiment is a modified commercially available HZSM-5 zeolite molecular sieve with a particle size of 2 mm. After the test, the catalyst was roasted at high temperature in the air first, and the residual coke was removed to regenerate the catalyst, and then the surface was treated with medical paraffin oil for the next test.
[0017] This example is mainly to investigate the effect of cracking temperature on the conversion rate of feedstock oil and the yield of refined bio-oil. The experiment is carried out at normal pressure and temperature range of 150°C to 600°C. Bio-oil obtained by rapid cracking of sawdust is used as feedstock oil. A catalytic cracking reactor with a catalytic bed size of Φ2×10 cm was used to compare the cracking conversion rate of raw oil and the yield of refined bio-oil at different temperatures. The results are shown in Table 1a. It can be seen from Table 1a that the conversion rate of feedstock oil and the yield of ref...
Embodiment 2
[0020] In the same apparatus as in Example 1, the particle diameter of the catalyst was 2.5 mm, and the reaction temperature was 380° C. This example is mainly to investigate the influence of feed amount to catalyst mass ratio (WHSV) on refined oil yield and raw oil conversion rate, and the results are shown in Table 2. It can be seen from Table 2 that the yield of refined oil increases correspondingly with the increase of WHSV at the beginning, reaching 50.0%, but the WHSV exceeds 3.5h -1 Finally, the yield of refined oil decreased slightly with the increase of WHSV. In addition, the chemical absorption method was used to analyze the non-condensable gas produced by the reaction, and the results showed that at WHSV≤4.5h -1 CO in gas 2 , CO content increased by 6.7% and 5.3% respectively, in other words, the oxygen in bio-oil 2 , The proportion of CO form removal increased. This is exactly what we want, because if O is replaced by H 2 The form of O is removed, and the H co...
Embodiment 3
[0022] In the same device of Example 1, the particle size of the catalyst used was changed and tested, and said catalyst was the same as in Example 1. This embodiment is mainly a comparative test done to compare the influence of the particle size of the catalyst on the reaction result, and the results are shown in Table 3. It can be seen from Table 3 that when the catalyst particle size is large, the effective catalytic activity of the catalyst is relatively low (more catalytic active centers are contained in the catalyst), so the yield of refined oil is low. For a catalyst with a diameter of 5.5 mm, the yield of refined oil is only 8.7%.
[0023] When the particle size of the catalyst is 2.5mm, the reaction temperature is 400°C, and the yield of refined oil can reach 47.8%. Therefore, the smaller particle size is beneficial to the reaction and can be selected within 1.5-4.5mm, but the particle size should be preferred 2.0-3.5mm catalyst. schedule
[0024] Table 1a ...
PUM
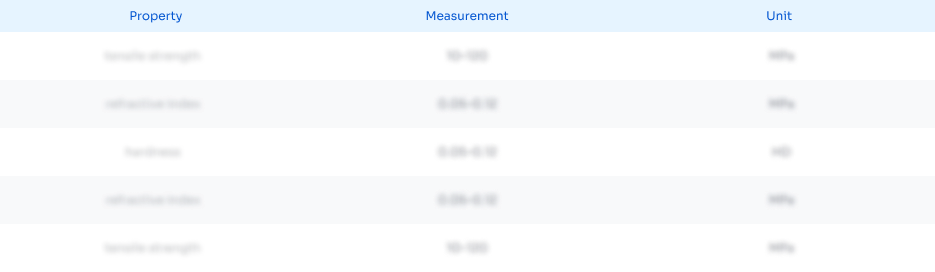
Abstract
Description
Claims
Application Information

- R&D
- Intellectual Property
- Life Sciences
- Materials
- Tech Scout
- Unparalleled Data Quality
- Higher Quality Content
- 60% Fewer Hallucinations
Browse by: Latest US Patents, China's latest patents, Technical Efficacy Thesaurus, Application Domain, Technology Topic, Popular Technical Reports.
© 2025 PatSnap. All rights reserved.Legal|Privacy policy|Modern Slavery Act Transparency Statement|Sitemap|About US| Contact US: help@patsnap.com