Organic compound fertilizer for flowers and plants
A kind of compound fertilizer and organic technology, applied in the field of organic compound fertilizer for flowers and its manufacture, can solve the problems of low absorption rate, slow release and long-term effect, low product strength, small particle strength, etc., to facilitate long-term storage and long-distance transportation , reduce the number of watering, good water absorption effect
- Summary
- Abstract
- Description
- Claims
- Application Information
AI Technical Summary
Problems solved by technology
Method used
Examples
Embodiment 1
[0017] Add 100kg of domestic sludge with 70% water content, 30kg of fermented rice husk powder, 30kg of fermented sheep dung powder, 2kg of superphosphate, and monoammonium phosphate into a two-wheel electric roller with a diameter of 1100mm and a power of 4kW. 1kg, urea 2kg, potassium sulfate 1kg, activated carbon 1kg, mixed and kneaded for 8 minutes, the material then enters a single-screw extruder (φ120mm, power 7.5kW, template hole diameter 5.0mm) and extrudes the material into smooth strips under a pressure of 8MPa Then the material is sent into the internal heat dryer (φ1200mm, length 26000m, speed 3 rpm) from the low temperature end, and the material entering the furnace is heated While rotating, the material is shaped, dehydrated, and the harmless treatment of the sludge is completed, and finally the temperature is raised to 100°C to produce granular organic compound fertilizer. Its organic matter content is 45%, and the product has no peculiar smell.
Embodiment 2
[0019] Add 100kg of domestic sludge with 80% water content, 40kg of fermented rice husk powder, 20kg of fermented straw powder, 5kg of monoammonium phosphate, 5kg of urea, and Potassium chloride 10kg, activated carbon 1.5kg, mixing and kneading for 10 minutes, the material then enters a single-screw extruder (φ120mm, power 7.5kW, template aperture 2.0mm) and extrudes the material into smooth strips under a pressure of 1MPa and immediately Cut into columnar particles, the ratio of length to diameter is 1:1, and then the material is sent from the low temperature end to the internal heating dryer (φ1200mm, length 26000m, speed 3 rpm), the material entering the furnace is heated while rotating, and the material Shaping, dehydration, and completing the harmless treatment of sludge, and finally raising the temperature to 150°C, and keeping the material in the furnace for 20 minutes to produce granular organic compound fertilizer. Its organic matter content is 50%, and the product ha...
Embodiment 3
[0021] Add 100kg of domestic sludge with 90% water content, 30kg of fermented rice husk powder, 6kg of fermented straw powder, and 4kg of fermented sheep dung powder into a two-wheel electric roller with a diameter of 1100mm and a power of 4kW. Calcium phosphate 4kg, diammonium phosphate 8kg, activated carbon 0.5kg, mixing and kneading for 10 minutes, the material then enters a single-screw extruder (φ120mm, power 7.5kW, template aperture 2.0mm) and extrudes the material into a smooth surface under a pressure of 1MPa. The strips are immediately cut into columnar particles with a length-to-diameter ratio of 1:1, and then the material is sent from the low-temperature end to the internal heat dryer (φ1200mm, length 26000m, speed 3 rpm), and the material side of the furnace Rotating while being heated, the material is shaped, dehydrated, and the harmless treatment of the sludge is completed, and finally the temperature is raised to 120°C to produce granular organic compound fertili...
PUM
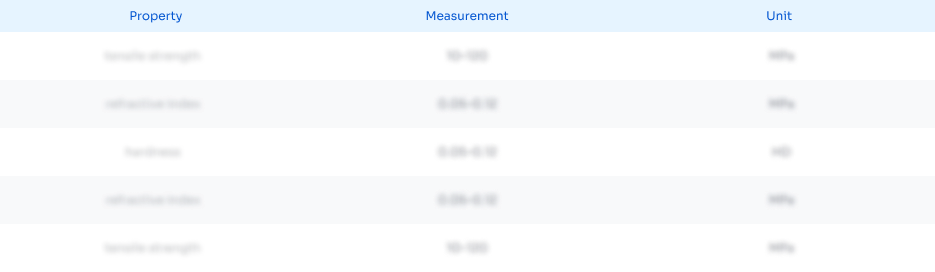
Abstract
Description
Claims
Application Information

- R&D
- Intellectual Property
- Life Sciences
- Materials
- Tech Scout
- Unparalleled Data Quality
- Higher Quality Content
- 60% Fewer Hallucinations
Browse by: Latest US Patents, China's latest patents, Technical Efficacy Thesaurus, Application Domain, Technology Topic, Popular Technical Reports.
© 2025 PatSnap. All rights reserved.Legal|Privacy policy|Modern Slavery Act Transparency Statement|Sitemap|About US| Contact US: help@patsnap.com