Surface fastener produced by molding synthetic resin integrally
An integral molding and synthetic resin technology, applied in fasteners, clothing, applications, etc., can solve the problems of reduced joint force, loss of surface fasteners, and easy fracture of the neck to achieve the effect of avoiding movement
- Summary
- Abstract
- Description
- Claims
- Application Information
AI Technical Summary
Problems solved by technology
Method used
Image
Examples
no. 1 example 1
[0064]The molded surface fastener 11 of this embodiment is characterized in that it has a fitting protrusion 6 . Like the first embodiment, the fitting protrusion 6 of this embodiment is also provided at the middle position of two engaging elements 3 adjacent in the width direction. The mating protrusion 6 includes a pair of elastic protrusions 6a, 6a protruding at a specific interval in the molding direction, and the outer surfaces of the two elastic protrusions 6a, 6a in the molding direction are inclined to the engaging element 3. The surface 3c basically has the inclined surface 6b at the same inclination angle.
[0065] In addition, the distance between the outer surfaces (inclined surfaces 6b, 6b) of the elastic protrusions 6a, 6a and the distance between the engaging heads 3b, 3b of the engaging elements 3, 3 located adjacent to the bottom ends thereof in the molding direction The gaps are substantially equal. In addition, the distance between the outer surfaces of th...
PUM
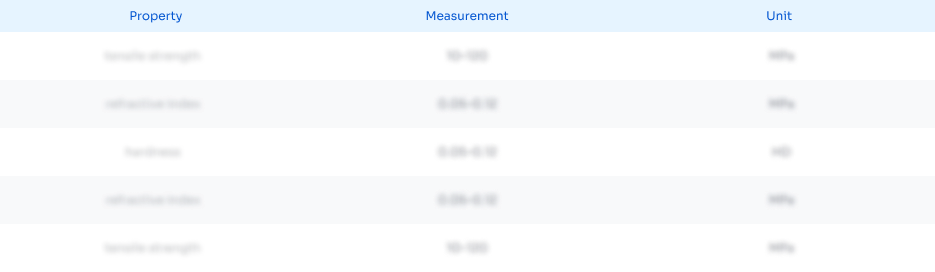
Abstract
Description
Claims
Application Information

- Generate Ideas
- Intellectual Property
- Life Sciences
- Materials
- Tech Scout
- Unparalleled Data Quality
- Higher Quality Content
- 60% Fewer Hallucinations
Browse by: Latest US Patents, China's latest patents, Technical Efficacy Thesaurus, Application Domain, Technology Topic, Popular Technical Reports.
© 2025 PatSnap. All rights reserved.Legal|Privacy policy|Modern Slavery Act Transparency Statement|Sitemap|About US| Contact US: help@patsnap.com