External active axial-shift compensating method and device for rotary main-shaft cutter
An active compensation and cutting tool technology, applied in metal processing, etc., can solve the problem of doubling the difficulty of equipment cost system control, etc., and achieve the effects of reducing the complexity of the spindle structure and manufacturing difficulty, good cutting quality, and low cost
- Summary
- Abstract
- Description
- Claims
- Application Information
AI Technical Summary
Problems solved by technology
Method used
Image
Examples
Embodiment Construction
[0016] The external active compensation method and device for the axial deflection of the spindle tool of the present invention mainly utilizes the active deflection control technology and is applied to the outside of the spindle, and the sensor outside the spindle directly measures the axial deflection of the tool, and the obtained measurement data As a feedback signal, it is used to control the cutting point of the tool to maintain the predetermined axial positioning accuracy. Since the components of the active compensation device of the present invention are added outside the main shaft in the form of additional components, it is not necessary to change the original structure of the original main shaft structure. In addition to greatly reducing the structural complexity and manufacturing difficulty of the main shaft, it is more cost-effective. Relatively low advantage, and can achieve better cutting quality. The device, method, action mode, and achievable effects of the pre...
PUM
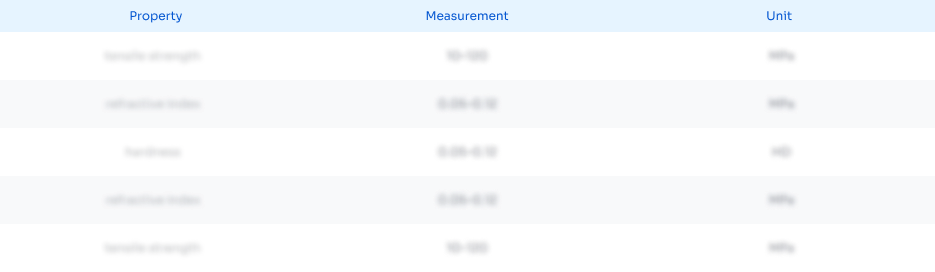
Abstract
Description
Claims
Application Information

- Generate Ideas
- Intellectual Property
- Life Sciences
- Materials
- Tech Scout
- Unparalleled Data Quality
- Higher Quality Content
- 60% Fewer Hallucinations
Browse by: Latest US Patents, China's latest patents, Technical Efficacy Thesaurus, Application Domain, Technology Topic, Popular Technical Reports.
© 2025 PatSnap. All rights reserved.Legal|Privacy policy|Modern Slavery Act Transparency Statement|Sitemap|About US| Contact US: help@patsnap.com