Cracking catalyst for reducing alkene content in catalytically cracked gasoline
A technology for catalytic cracking gasoline and cracking catalyst, which is used in catalytic cracking, physical/chemical process catalyst, molecular sieve catalyst, etc., can solve the problem of high cost of molecular sieve, and achieve the effect of reducing gasoline olefin content and excellent heavy oil conversion ability
- Summary
- Abstract
- Description
- Claims
- Application Information
AI Technical Summary
Problems solved by technology
Method used
Image
Examples
Embodiment 1
[0028] Take 18.6 kg of NaY molecular sieve (Changling Oil Refinery Catalyst Plant, ignition loss 24.9% by weight, silicon to aluminum ratio of 5.2) and 140 kg of deionized water are added to the reactor, and then 2.1 kg of ammonium sulfate is added to it, 90°C After stirring for 5 minutes, adjust the pH of the system to between 3.5 and 5.5 with hydrochloric acid, continue stirring for 1 hour and then filter. Add 140 kilograms of water to the filter cake, then add 5.3 kilograms of solid lanthanum chloride, stir at 90°C for 2 hours, add 1.5 kilograms of sodium metaaluminate solution and 1.2 kilograms of ammonia, stir for 5 minutes, filter, wash with water, air-dried, and enter the roaster , At a weight airspeed of 0.5 -1 It is calcined at 550°C for 1.5 hours under high water vapor, and the molecular sieve obtained after cooling is referred to as CDY-1A. The molecular sieve: ammonium chloride: water=1:0.1:10 is washed with ammonium chloride solution at 60°C for 10 minutes, and dried ...
Embodiment 2
[0032] Take 18.6 kg of NaY molecular sieve (Changling Oil Refinery Catalyst Plant, ignition loss 24.9% by weight, silicon to aluminum ratio of 5.2) and 140 kg of deionized water are added to the reactor, and then 2.1 kg of ammonium sulfate is added to it, 90°C After stirring for 5 minutes, adjust the pH of the system to between 3.5 and 5.5 with hydrochloric acid, continue stirring for 1 hour and then filter. Add 140 kg of water to the filter cake, then add 10.4 liters of rare earth chloride solution (the concentration of rare earth oxide is 312 g / liter, the same below), stir at room temperature for 5 minutes, adjust the pH of the system to between 3.5 and 5.5 with hydrochloric acid, continue After stirring for 1 hour, add 2.2 kilograms of water glass solution and 1.3 kilograms of ammonia, stir for 5 minutes, filter, wash with water, air-dried, enter the roaster, roast at 550°C for 1.5 hours, and cool down to obtain molecular sieve as CDY-2A, and then press molecular sieve : Ammoni...
Embodiment 3
[0036] Take 46.6 kilograms of NaY molecular sieve slurry (Qilu Catalyst Factory, NaY concentration is 30.0% by weight, NaY silicon-aluminum ratio is 5.1) and 80 kilograms of deionized water are added to the reactor, and then 5.3 liters of rare earth chloride solution is added to it. After stirring for 5 minutes at ℃, adjust the pH of the system to between 3.5 and 5.5 with hydrochloric acid. After stirring for 1 hour, add 1.6 kg of ammonia water, stir for 5 minutes, filter, wash with water, air-dried, and enter the roaster at a weight space velocity of 0.2 o'clock. -1 It is calcined at 600°C for 1.5 hours under high water vapor, and the molecular sieve obtained after cooling is recorded as CDY-3A, and then washed with ammonium chloride solution at 90°C for 10 minutes at the ratio of molecular sieve: ammonium chloride: water = 1:0.1:10, and dried to obtain The finished molecular sieve is numbered CDY-3.
[0037] According to fluorescence method, the content of rare earth oxide in CD...
PUM
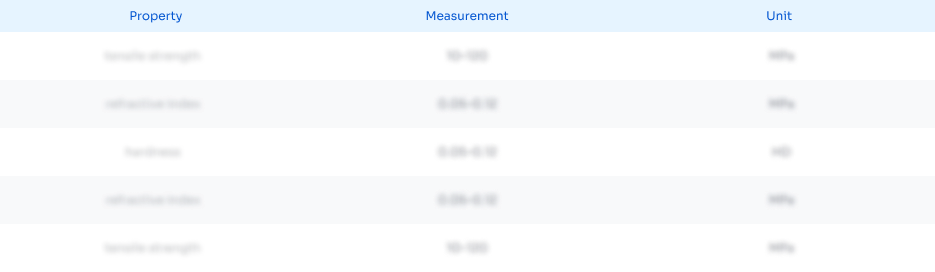
Abstract
Description
Claims
Application Information

- R&D
- Intellectual Property
- Life Sciences
- Materials
- Tech Scout
- Unparalleled Data Quality
- Higher Quality Content
- 60% Fewer Hallucinations
Browse by: Latest US Patents, China's latest patents, Technical Efficacy Thesaurus, Application Domain, Technology Topic, Popular Technical Reports.
© 2025 PatSnap. All rights reserved.Legal|Privacy policy|Modern Slavery Act Transparency Statement|Sitemap|About US| Contact US: help@patsnap.com