Catalytic cracking process for preparing high-grade gasoline
A gasoline and heavy gasoline technology, applied in catalytic cracking, cracking, petroleum industry, etc., to improve gasoline quality, reduce cracking reactions, and improve desulfurization effects
- Summary
- Abstract
- Description
- Claims
- Application Information
AI Technical Summary
Problems solved by technology
Method used
Image
Examples
Embodiment 1
[0041] This embodiment illustrates that the method provided by the present invention can obtain a good gasoline upgrading effect, and the gasoline yield is relatively high.
[0042] The feed oil and catalyst entering the cracking reactor are the same as those in Comparative Example 1. The outlet temperature of the riser reactor is 500°C, the lower temperature of the gasoline upgrading riser reaction section is 580°C, and the upper temperature is 490°C, dense phase fluidized bed The bed temperature is 420°C, other operating conditions are listed in Table 3, the product distribution is listed in Table 4, Table 5 lists the properties of gasoline, and the gasoline composition analysis is listed in Table 6.
[0043] Compared with the comparative example, when the raw materials are the same, Example 1 adopts the combined process of the present invention to increase the conversion rate of heavy oil raw materials by 2.30% (to the raw materials), and increase the liquefied gas yield by 2.2...
Embodiment 2
[0045] This embodiment illustrates that the method provided by the present invention can obtain a good gasoline upgrading effect, and the gasoline yield is relatively high.
[0046] The feed oil entering the cracking reactor is the same as that of Comparative Example 1. The outlet temperature of the riser reactor is 505°C, the lower temperature of the gasoline upgrading riser reaction section is 540°C, and the upper temperature is 450°C. The dense fluidized bed layer The temperature is 380°C, other operating conditions are listed in Table 3, the product distribution is listed in Table 4, Table 5 lists the properties of gasoline, and the gasoline composition analysis is listed in Table 6. The catalyst B used in Example 2 is slightly different from the catalyst used in the comparative example, and basically belongs to the same type of catalyst.
[0047]Compared with the comparative example, when the raw materials are the same, Example 2 adopts the combined process of the present inv...
Embodiment 3
[0049] This embodiment illustrates that the method provided by the present invention can obtain a good gasoline upgrading effect, and the gasoline yield is relatively high.
[0050] The feed oil and catalyst entering the cracking reactor are the same as those in Comparative Example 1. The outlet temperature of the riser reactor is 500°C, the lower temperature of the gasoline upgrading riser reaction section is 510°C, and the upper temperature is 420°C, dense phase fluidized bed The bed temperature is 350°C, other operating conditions are listed in Table 3, the product distribution is also listed in Table 4, Table 5 lists the properties of gasoline, and the gasoline composition analysis is listed in Table 6.
[0051] Compared with the comparative example, when the raw materials are the same, Example 3 adopts the combined process of the present invention to increase the conversion rate of heavy oil raw materials by 2.38% (to the raw materials), and increase the liquefied gas yield b...
PUM
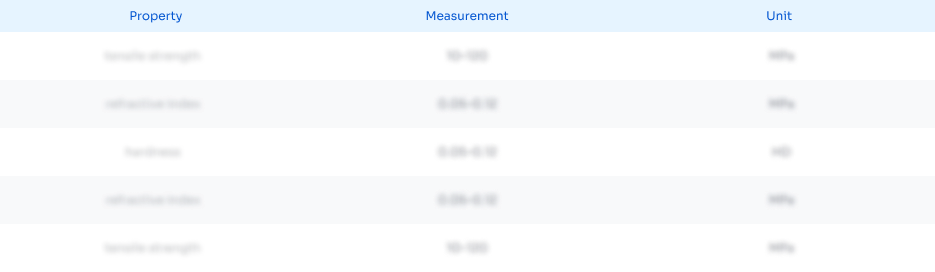
Abstract
Description
Claims
Application Information

- Generate Ideas
- Intellectual Property
- Life Sciences
- Materials
- Tech Scout
- Unparalleled Data Quality
- Higher Quality Content
- 60% Fewer Hallucinations
Browse by: Latest US Patents, China's latest patents, Technical Efficacy Thesaurus, Application Domain, Technology Topic, Popular Technical Reports.
© 2025 PatSnap. All rights reserved.Legal|Privacy policy|Modern Slavery Act Transparency Statement|Sitemap|About US| Contact US: help@patsnap.com