Dynamic testing loading unit for MEMS disc or device
A technology of dynamic testing and loading devices, which is applied in the direction of measuring devices, electrical devices, microstructure devices, etc. It can solve the problems of being unsuitable for dynamic testing of small specimens, unsuitable for dynamic testing of MEMS wafers or devices, etc., and achieves a controllable Effect
- Summary
- Abstract
- Description
- Claims
- Application Information
AI Technical Summary
Problems solved by technology
Method used
Image
Examples
Embodiment Construction
[0012] Depend on figure 1 and figure 2 As shown, a dynamic test loading device for a MEMS wafer or device includes a light-transmitting sheet 9, a cavity 1, a bracket 5 and a support plate 13, and a sealing ring 7 is placed between the light-transmitting sheet 9 and the opening end face of the cavity 1 , and connected to the flange 16 through the sealing ring 8, the flange 16 is fixed to the opening end face of the vacuum chamber 1 through the bolt 17 and the nut 18, the light-transmitting sheet 9 and the chamber 1 form a sealed chamber, which is a MEMS circle for dynamic testing chip or device to provide a closed environment.
[0013] An electrode 21 is installed on the cavity 1, and an air charging port 6, a vacuum port 20 and a vacuum gauge interface 22 are opened. The bracket 5 can be fixed on the base of the cavity 1 by bolts 2, and the adjusting screw 3 is installed in the base of the bracket 5. , the piezoelectric ceramic (PZT) 4 is placed in the bracket 5, the lower...
PUM
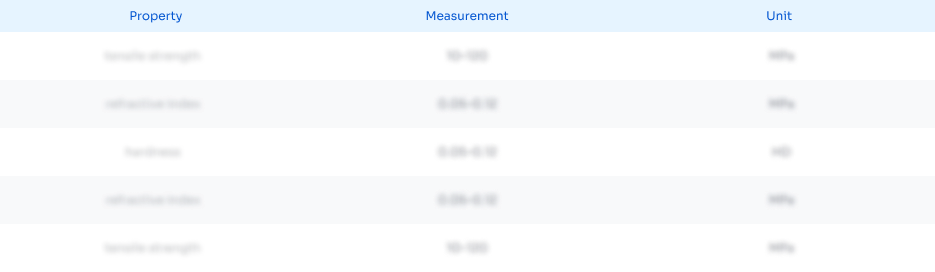
Abstract
Description
Claims
Application Information

- Generate Ideas
- Intellectual Property
- Life Sciences
- Materials
- Tech Scout
- Unparalleled Data Quality
- Higher Quality Content
- 60% Fewer Hallucinations
Browse by: Latest US Patents, China's latest patents, Technical Efficacy Thesaurus, Application Domain, Technology Topic, Popular Technical Reports.
© 2025 PatSnap. All rights reserved.Legal|Privacy policy|Modern Slavery Act Transparency Statement|Sitemap|About US| Contact US: help@patsnap.com