Method for fabricating improved composite active black dyestuff
A manufacturing method and reactive black technology, applied in the field of dyes, can solve the problems of unfavorable environmental protection, insufficient lifting force, large amount of sewage, etc., and achieve the effect of reducing water consumption in production and application, improving solubility, and reducing the generation of sewage
- Summary
- Abstract
- Description
- Claims
- Application Information
AI Technical Summary
Problems solved by technology
Method used
Image
Examples
Embodiment 1
[0020] Embodiment 1, the improved compound reactive black dye manufacture method, after mixing 75 parts of reactive navy blue solution and 25 parts of reactive orange solution of synthesis, spray drying to obtain finished product.
Embodiment 2
[0021] Embodiment 2, the improved composite reactive black dye manufacturing method, after mixing 65 parts of reactive navy blue solutions, 30 parts of reactive orange solutions, and 5 parts of reactive red solutions and stirring evenly, spray drying to obtain finished products, wherein when synthesizing reactive navy blue, raw materials The proportioning ratio of H acid and p-(β-sulfate ethyl sulfone) aniline is controlled to be 0.35:1.
Embodiment 3
[0022] Embodiment 3, the improved compound reactive black dyestuff manufacturing method, after 80 parts of reactive navy blue solutions of synthesis, 18 parts of reactive orange solutions and 2 parts of reactive red solutions after nano-membrane treatment are mixed and stirred, spray-dried to obtain finished product, wherein When synthesizing active navy blue, the feed ratio of raw material H acid and p-(β-sulfate ethyl sulfone) aniline is controlled to 0.4:1, and nano-membrane concentration is carried out.
PUM
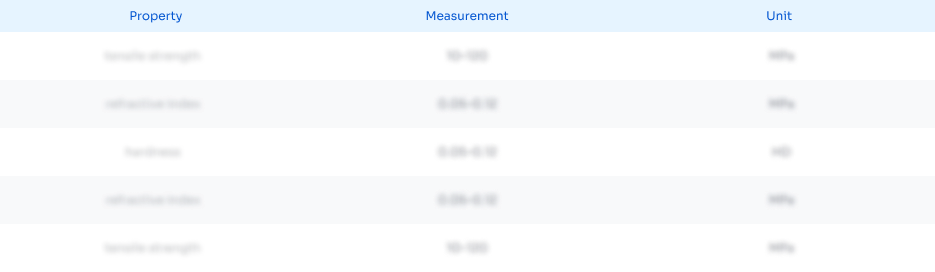
Abstract
Description
Claims
Application Information

- R&D Engineer
- R&D Manager
- IP Professional
- Industry Leading Data Capabilities
- Powerful AI technology
- Patent DNA Extraction
Browse by: Latest US Patents, China's latest patents, Technical Efficacy Thesaurus, Application Domain, Technology Topic, Popular Technical Reports.
© 2024 PatSnap. All rights reserved.Legal|Privacy policy|Modern Slavery Act Transparency Statement|Sitemap|About US| Contact US: help@patsnap.com