Method for mfg. of strips of stainless steel and integrated rolling mill line
A technology for stainless steel strips and rolling lines, which can be used in metal rolling, metal rolling, manufacturing tools, etc., and can solve complex problems
- Summary
- Abstract
- Description
- Claims
- Application Information
AI Technical Summary
Problems solved by technology
Method used
Image
Examples
Embodiment Construction
[0011] In the accompanying drawings, Figure 1A schematically shows some different methods for producing stainless steel strip, preferably austenitic stainless steel strip or ferritic stainless steel strip, which constitutes the required later Figure 1B Raw material processed in rolling lines in Figure 1B The rolling line B is used to implement the method involved in the present invention. Ferritic-austenitic steel strip is also possible. Three methods for producing the starting material are shown in Figure 1A. According to method I, the slab 1 is hot-rolled in a hot-rolling line to produce a hot-rolled strip having a thickness conventional for hot-rolled strip, ie 1.5-6 mm. According to one aspect of the invention, the hot rolling is stopped before or at the latest when the thickness has dropped to 2.5 mm, i.e. to obtain a strip with a thickness between 3-6 mm, preferably at Between 3mm and 5mm. In a quenching section 3 the hot-rolled strip can be quenched to a temperatu...
PUM
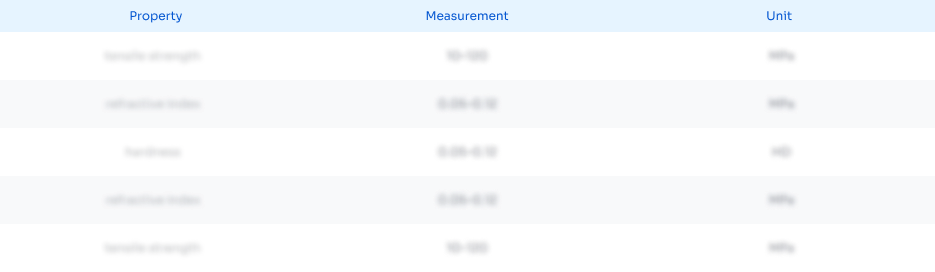
Abstract
Description
Claims
Application Information

- R&D Engineer
- R&D Manager
- IP Professional
- Industry Leading Data Capabilities
- Powerful AI technology
- Patent DNA Extraction
Browse by: Latest US Patents, China's latest patents, Technical Efficacy Thesaurus, Application Domain, Technology Topic, Popular Technical Reports.
© 2024 PatSnap. All rights reserved.Legal|Privacy policy|Modern Slavery Act Transparency Statement|Sitemap|About US| Contact US: help@patsnap.com