Robot joint combined sealing structure
A robot joint and combined sealing technology, which is applied to manipulators, program-controlled manipulators, manufacturing tools, etc., can solve the problems of joint seal reliability and installation difficulties, and achieve the effects of long service life, consistency and reliability
- Summary
- Abstract
- Description
- Claims
- Application Information
AI Technical Summary
Problems solved by technology
Method used
Image
Examples
Embodiment 1
[0029] see Figure 1 to Figure 2 , figure 1 Shown is a typical robot joint structure, which is provided with a first moving member 1, a second moving member 2, a reduction gear 3, a joint combined oil seal 4, a motor 5, and a reduction gear input gear 6. The motor 5 drives the deceleration device 3 to output and rotate through the deceleration device input gear 6 . The joint combination oil seal 4 is provided between the second moving member 2 and the reduction gear 3 . like figure 2 As shown, the joint combined oil seal 4 includes two parts, a skeleton bushing 4-1 and a sealing ring 4-2. The inner side of the skeleton bushing 4-1 is provided with an elastic sealing ring 4-11, the elastic sealing ring 4-11 and the reduction gear 3 The housing is in static sealing contact. The elastic sealing ring 4-11 is made of elastic sealing material, which can effectively prevent the leakage of grease in the cavity and the entry of external pollutants through the gap between the skele...
Embodiment 2
[0033] Basically the same as the embodiment, the difference is that the frame of the frame bushing 4-1 includes the structure of the flange edge 4-12 (such as image 3 shown), an annular end face sealing lip 4-21 is provided on the outer end surface of the sealing ring 4-2, and the end face sealing lip 4-21 is in sealing contact with the flange edge 4-12 of the skeleton bushing to further enhance the sealing effect.
Embodiment 3
[0035] It is basically the same as the embodiment, the difference is that the sealing ring 4-2 adopts the Figure 4 Double main lip skeleton oil seal shown. For the present invention, the sealing ring 4-2 may also be a Y-shaped ring, an A-shaped ring, a B-shaped ring or a C-shaped ring.
PUM
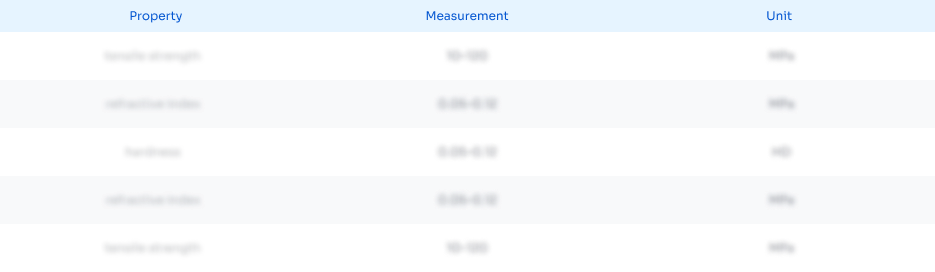
Abstract
Description
Claims
Application Information

- R&D Engineer
- R&D Manager
- IP Professional
- Industry Leading Data Capabilities
- Powerful AI technology
- Patent DNA Extraction
Browse by: Latest US Patents, China's latest patents, Technical Efficacy Thesaurus, Application Domain, Technology Topic, Popular Technical Reports.
© 2024 PatSnap. All rights reserved.Legal|Privacy policy|Modern Slavery Act Transparency Statement|Sitemap|About US| Contact US: help@patsnap.com