AGV configuration optimization method based on simulation particle swarm optimization
A particle swarm algorithm and configuration optimization technology, applied in the direction of calculation, calculation model, data processing application, etc., can solve the problems of abnormal difficulty, high AGV configuration cost, unstable production system efficiency, etc., to reduce blockage, reduce cost, improve The effect of production efficiency
- Summary
- Abstract
- Description
- Claims
- Application Information
AI Technical Summary
Problems solved by technology
Method used
Image
Examples
Embodiment 1
[0088] like Figure 1-Figure 3 As shown, the present invention provides an AGV configuration optimization method based on a simulated particle swarm algorithm, which specifically includes the following steps:
[0089] S1. Build a simulation model of the actual production environment.
[0090] S2. Establish a mathematical model for AGV configuration optimization and set constraint parameter conditions.
[0091] S3. Use the simulation model to improve the particle swarm algorithm to obtain the improved particle swarm algorithm; calculate the fitness value of the particle by using the constraint parameter condition.
[0092] S4. Use the improved particle swarm algorithm to solve the mathematical model of the AGV configuration optimization, and obtain the optimized AGV configuration.
[0093] First build a simulation model that simulates the production process of the production system, establish a mathematical model for AGV configuration optimization and set constraint parameter...
Embodiment 2
[0165] Based on the above Embodiment 1, this embodiment describes in detail the specific process of using the simulation model to improve the particle swarm algorithm.
[0166] First, using the monotonic characteristic to obtain the required quantity of each AGV when only one AGV is considered through simulation, the obtained quantity is set as the upper bound of the solution space of this type of AGV.
[0167] Further, initialize the particle swarm, realize the data exchange between Plant simulation and pycharm according to the TCP / IP protocol, and then input the upper bound obtained above into the particle swarm algorithm as the upper bound of the solution space, and the lower bound is set to 0, that is, it is not used. Class AGV. Next, the position and velocity within a certain range are generated in the solution space and assigned to each particle to obtain the initial population, and the position and velocity of the ith particle in the particle population are recorded.
...
Embodiment 3
[0175] like Figure 4 As shown, this embodiment provides an AGV configuration optimization system based on a simulated particle swarm algorithm, characterized in that the system includes: a memory and a processor, and the memory includes a program for an AGV configuration optimization method based on the simulated particle swarm algorithm , the AGV configuration optimization method program based on the simulated particle swarm algorithm is executed by the processor to achieve the following steps:
[0176] S1. Build a simulation model of the actual production environment;
[0177] S2. Establish a mathematical model for AGV configuration optimization and set constraint parameter conditions;
[0178] S3, using the simulation model to improve the particle swarm algorithm to obtain the improved particle swarm algorithm; using the constraint parameter condition to calculate the fitness value of the particle;
[0179] S4. Use the improved particle swarm algorithm to solve the mathe...
PUM
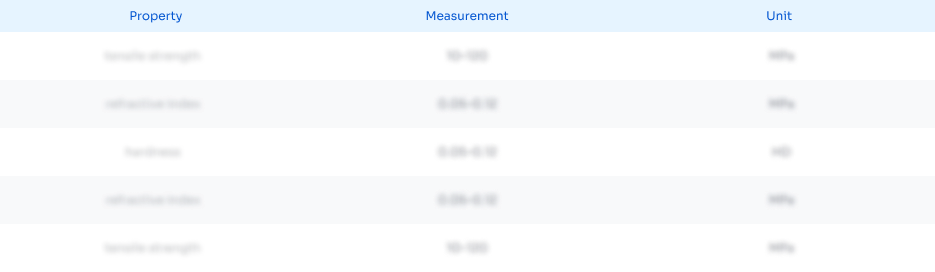
Abstract
Description
Claims
Application Information

- R&D Engineer
- R&D Manager
- IP Professional
- Industry Leading Data Capabilities
- Powerful AI technology
- Patent DNA Extraction
Browse by: Latest US Patents, China's latest patents, Technical Efficacy Thesaurus, Application Domain, Technology Topic, Popular Technical Reports.
© 2024 PatSnap. All rights reserved.Legal|Privacy policy|Modern Slavery Act Transparency Statement|Sitemap|About US| Contact US: help@patsnap.com