High-speed motorized spindle thermoelastic deformation simulation method and system based on boundary element model
A high-speed electro-spindle and simulation method technology, applied in the direction of constraint-based CAD, electro-digital data processing, instruments, etc., can solve the problems of unable to give full play to the advantages of the algorithm, large amount of calculation, ignoring the pressure distribution, etc., and achieve simple node division steps. , the effect of strong versatility and improved computing efficiency
- Summary
- Abstract
- Description
- Claims
- Application Information
AI Technical Summary
Problems solved by technology
Method used
Image
Examples
Embodiment Construction
[0038] The present invention will be further described below with reference to the accompanying drawings and embodiments.
[0039] like figure 1 As shown, a method for simulating thermoelastic deformation of a high-speed motorized spindle based on a boundary element model includes the following steps:
[0040] Step 1: Build a simplified 2D model of the high-speed motorized spindle.
[0041] like figure 2 As shown in the figure, the 1 / 4 plane of the high-speed motorized spindle is intercepted as an axisymmetric two-dimensional model, and the model of the intercepted two-dimensional plane model is simplified, including the detailed features of the high-speed motorized spindle, such as small holes, shallow grooves, tiny bosses, Delete the chamfers, undercuts and transition arcs at the shaft end; delete sensors, wires and sealing rings that are light in weight and do not bear stress; , which are merged with the housing and the main shaft respectively; the built-in motor struct...
PUM
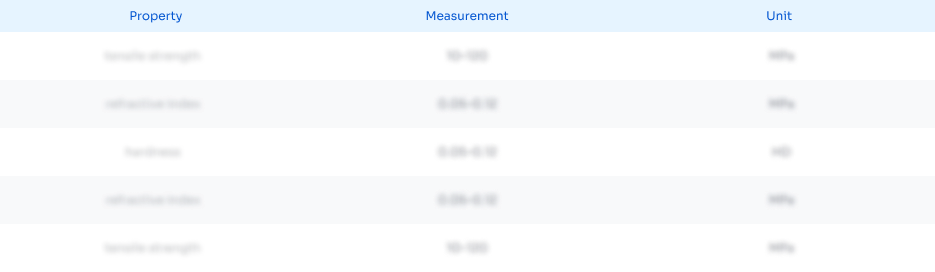
Abstract
Description
Claims
Application Information

- R&D
- Intellectual Property
- Life Sciences
- Materials
- Tech Scout
- Unparalleled Data Quality
- Higher Quality Content
- 60% Fewer Hallucinations
Browse by: Latest US Patents, China's latest patents, Technical Efficacy Thesaurus, Application Domain, Technology Topic, Popular Technical Reports.
© 2025 PatSnap. All rights reserved.Legal|Privacy policy|Modern Slavery Act Transparency Statement|Sitemap|About US| Contact US: help@patsnap.com