Electric vehicle shell machining method
A processing method and technology for electric vehicles, applied in the field of automobile gearbox processing, can solve the problems of mismatch of three-face process rhythm, dimensional stability production, single processing method, etc., to improve the overall efficiency of equipment, improve flatness, ensure consistent effect
- Summary
- Abstract
- Description
- Claims
- Application Information
AI Technical Summary
Problems solved by technology
Method used
Image
Examples
Embodiment 1
[0020] see figure 1 A method for machining an electric vehicle casing of the present invention is shown, and the steps are as follows:
[0021] 1) Determine the processing surface of the shell: the shell has four surfaces that need to be processed, the upper and lower planes and the two peripheral boss surfaces, and the two peripheral boss surfaces have a 30° installation angle with each other;
[0022] 2) The shell is processed through two processes:
[0023] a. Process 1: When installing a boss on the periphery of the part, ensure that it is perpendicular to the machining tool, and machine the upper and lower planes of the shell, the high-precision hole and the side in one direction at one time;
[0024] b. Process 2: Deflect the part by 30° to be perpendicular to the machining tool, and process the side surface and the remaining apertures of the upper and lower planes in the other direction relative to the process 1;
[0025] 3) Carry out high pressure cleaning and low pr...
Embodiment 2
[0030] like figure 1 A method for machining an electric vehicle casing of the present invention is shown, and the steps are as follows:
[0031] 1) Determine the processing surface of the shell: the shell has four surfaces that need to be processed, the upper and lower planes and the two peripheral boss surfaces, and the two peripheral boss surfaces have a 30° installation angle with each other;,
[0032] 2) The shell is processed through two processes:
[0033] a. Process 1: When installing a boss on the periphery of the part, ensure that it is perpendicular to the machining tool, and machine the upper and lower planes of the shell, the high-precision hole and the side in one direction at one time;
[0034] b. Process 2: Deflect the part by 30° to be perpendicular to the machining tool, and process the side surface and the remaining apertures of the upper and lower planes in the other direction relative to the process 1;
[0035] 3) Carry out high pressure cleaning and low ...
PUM
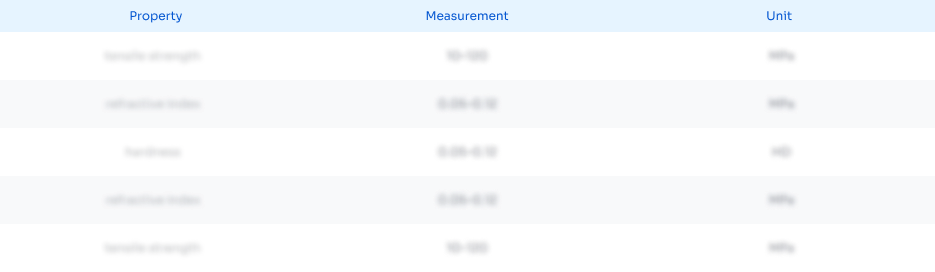
Abstract
Description
Claims
Application Information

- Generate Ideas
- Intellectual Property
- Life Sciences
- Materials
- Tech Scout
- Unparalleled Data Quality
- Higher Quality Content
- 60% Fewer Hallucinations
Browse by: Latest US Patents, China's latest patents, Technical Efficacy Thesaurus, Application Domain, Technology Topic, Popular Technical Reports.
© 2025 PatSnap. All rights reserved.Legal|Privacy policy|Modern Slavery Act Transparency Statement|Sitemap|About US| Contact US: help@patsnap.com