Industrial robot joint friction compensation method based on disturbance observation
A technology of industrial robots and disturbance observers, applied in manipulators, manufacturing tools, program-controlled manipulators, etc., can solve problems such as deterioration of friction compensation effects and inconsistencies in observer performance, and achieve improved synchronization and rhythm, good results, and improved Effects of Accuracy and Smoothness
- Summary
- Abstract
- Description
- Claims
- Application Information
AI Technical Summary
Problems solved by technology
Method used
Image
Examples
Embodiment 1
[0055] see figure 1 , the present embodiment discloses a method for compensating the joint friction of an industrial robot based on disturbance observation, including the following contents:
[0056] 1) Collect the motor rotor angle θ of each joint motor encoder mi ;
[0057] 2) Set the rotor angle θ of each joint motor mi Input the moment of inertia calculation module, which outputs the moment of inertia of the total load converted to the motor side by each joint i J l ;
[0058] 3) Set the total load moment of inertia on the motor side i J l and the motor rotor angle θ mi Enter the disturbance observer module to get the observed value of the friction torque
[0059] 4) The observed value of friction torque Multiply the compensation coefficient k c Get the compensation torque T ci ;
[0060] 5) will compensate torque T ci Converted to friction compensation current I ci , if the T ci divided by the torque-current conversion factor k t ,Right now or the T ...
PUM
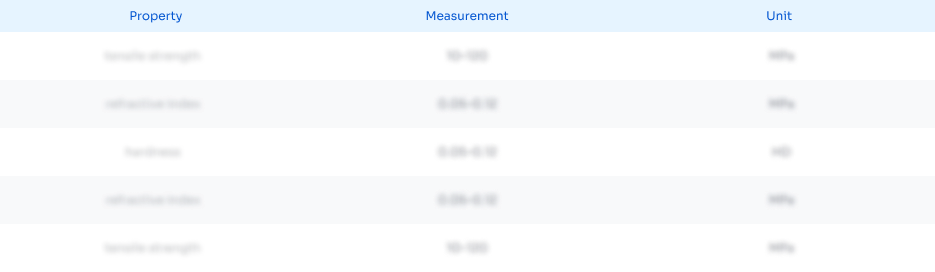
Abstract
Description
Claims
Application Information

- R&D Engineer
- R&D Manager
- IP Professional
- Industry Leading Data Capabilities
- Powerful AI technology
- Patent DNA Extraction
Browse by: Latest US Patents, China's latest patents, Technical Efficacy Thesaurus, Application Domain, Technology Topic, Popular Technical Reports.
© 2024 PatSnap. All rights reserved.Legal|Privacy policy|Modern Slavery Act Transparency Statement|Sitemap|About US| Contact US: help@patsnap.com