Stamping die for metal plate stamping
A stamping die and sheet metal technology, applied in the direction of manufacturing tools, metal processing equipment, feeding devices, etc., can solve the problems of increasing the risk factor of the staff and increasing the workload of the staff, so as to reduce the probability of adhesion and improve The rate of fall, the effect of reducing workload
- Summary
- Abstract
- Description
- Claims
- Application Information
AI Technical Summary
Problems solved by technology
Method used
Image
Examples
Embodiment 1
[0031] like Figure 1 to Figure 2 As shown, a stamping die for sheet metal stamping according to an embodiment of the present invention includes an upper die 1, a lower die 2, a support table 3 and a pusher assembly; a plurality of punches are installed on the bottom surface of the upper die 1 4. The metal sheet 5 is slidably mounted on the top groove of the lower mold 2, and a plurality of waste holes 6 are opened on the bottom surface of the top groove of the lower mold 2. The waste holes 6 penetrate through the lower mold 2, and the waste holes The inner wall of 6 is slidingly matched with the outer wall of the punch 4, the bottom surfaces of both sides of the lower die 2 are fixedly connected to the support table 3, and one side of the lower die 2 is installed with a pusher assembly; the pusher assembly includes a push plate 7 and transmission unit, a push plate 7 is slidably installed between the support platforms 3 on both sides, the top surface of the push plate 7 is sl...
Embodiment 2
[0041] like Figure 8 As shown in the comparison example 1, another embodiment of the present invention is that: the oblique angle of the push knife 44 is provided with a plurality of turning grooves 48, the inside of the turning groove 48 is rotated to install the turning plate 49, and the turning The bottom surface of the plate 49 is fixed to a plurality of No. 6 springs 50, and the bottom end of the No. 6 springs 50 is fixed to the inner wall of the turning slot 48. The cross section of the turning plate 49 is semi-conical, and the The bottom end coincides with the bottom end of the rotating groove 48, and the top of the rotating plate 49 is located outside the rotating groove 48, and the rotating shaft of the rotating plate 49 is located on the top of the rotating plate 49 close to the side of the rotating groove 48; when in use, push the knife When 44 is inserted into the bottom of the metal sheet 5, the metal sheet 5 slides up along the oblique angle of the pusher 44, an...
PUM
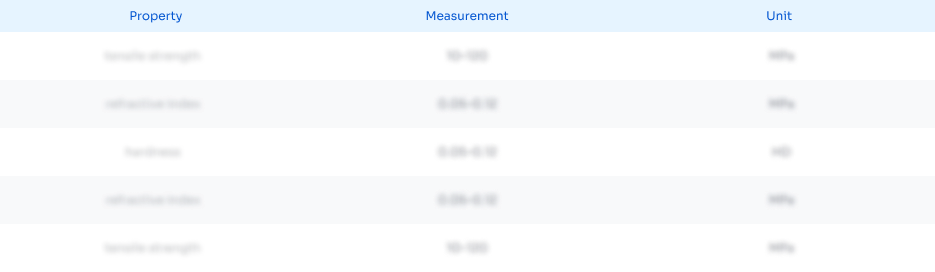
Abstract
Description
Claims
Application Information

- R&D Engineer
- R&D Manager
- IP Professional
- Industry Leading Data Capabilities
- Powerful AI technology
- Patent DNA Extraction
Browse by: Latest US Patents, China's latest patents, Technical Efficacy Thesaurus, Application Domain, Technology Topic, Popular Technical Reports.
© 2024 PatSnap. All rights reserved.Legal|Privacy policy|Modern Slavery Act Transparency Statement|Sitemap|About US| Contact US: help@patsnap.com