Series robot control system and calibration method
A technology for controlling systems and robots, applied in the direction of program-controlled manipulators, manipulators, manufacturing tools, etc., can solve problems such as the inability to set target positions, and achieve the effects of improving system reliability, simplifying system hardware, and reducing hardware costs
- Summary
- Abstract
- Description
- Claims
- Application Information
AI Technical Summary
Problems solved by technology
Method used
Image
Examples
Embodiment Construction
[0042] Embodiments of the present invention will be described in further detail below in conjunction with the accompanying drawings.
[0043] A series robot control system of the present invention comprises a controller and an n-axis series drive module;
[0044] The n-axis serial drive module is respectively connected to the n axes of the n-axis serial robot, and is controlled by the controller to realize the driving of the robot arm;
[0045] Each axis series drive module includes a set of series drives, stepper motors, encoders and reducers;
[0046] see figure 1 , taking a three-axis serial robot as an example, the control system includes a controller, a driver 1, a stepping motor 1, an encoder 1, a reducer 1, a driver 2, a stepping motor 2, an encoder 2, a reducer 2, a driver 3. Stepper motor 3, encoder 3, reducer 3, etc.
[0047] The controller completes the inverse calculation of the robot, and transmits the calculated results to the driver 1, the driver 2, and the d...
PUM
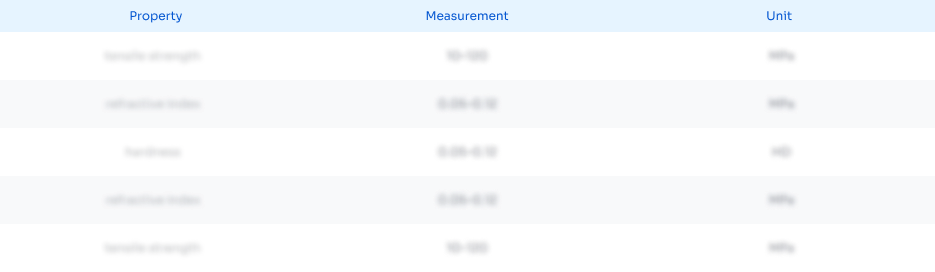
Abstract
Description
Claims
Application Information

- Generate Ideas
- Intellectual Property
- Life Sciences
- Materials
- Tech Scout
- Unparalleled Data Quality
- Higher Quality Content
- 60% Fewer Hallucinations
Browse by: Latest US Patents, China's latest patents, Technical Efficacy Thesaurus, Application Domain, Technology Topic, Popular Technical Reports.
© 2025 PatSnap. All rights reserved.Legal|Privacy policy|Modern Slavery Act Transparency Statement|Sitemap|About US| Contact US: help@patsnap.com