Experimental measurement system and method for dynamic characteristic coefficient of annular dynamic seal
A technology of dynamic characteristics and measurement system, which is used in aerodynamic tests, measurement devices, complex mathematical operations, etc., can solve problems such as poor measurement accuracy, inability to measure dynamic characteristic coefficients, and inability to obtain seal dynamic characteristic coefficients, and to ensure uniformity. the effect of reducing the risk of torsional vibration
- Summary
- Abstract
- Description
- Claims
- Application Information
AI Technical Summary
Problems solved by technology
Method used
Image
Examples
Embodiment Construction
[0063] In order to illustrate the objectives, technical solutions and technical advantages of the present invention more clearly, the present invention will be further described in detail below with reference to the accompanying drawings and examples. Obviously, the described embodiments are part of the embodiments of the present invention, and are intended to be used to explain the present invention, but should not be construed as a limitation of the present invention. Based on the embodiments disclosed in the present invention, other embodiments obtained by those of ordinary skill in the art without creative work all belong to the protection scope of the present invention.
[0064] see figure 1 , figure 2 , image 3 and Figure 4 , An annular dynamic seal dynamic characteristic coefficient experimental measurement system according to an embodiment of the present invention includes: a dynamic seal experimental section, an air supply system, a drive system, a vibration exc...
PUM
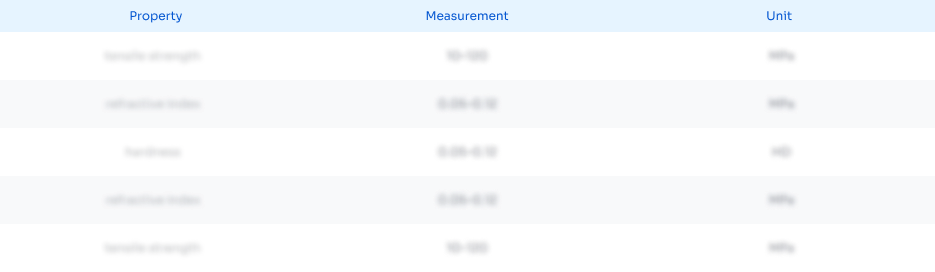
Abstract
Description
Claims
Application Information

- R&D Engineer
- R&D Manager
- IP Professional
- Industry Leading Data Capabilities
- Powerful AI technology
- Patent DNA Extraction
Browse by: Latest US Patents, China's latest patents, Technical Efficacy Thesaurus, Application Domain, Technology Topic, Popular Technical Reports.
© 2024 PatSnap. All rights reserved.Legal|Privacy policy|Modern Slavery Act Transparency Statement|Sitemap|About US| Contact US: help@patsnap.com