Dynamic crosslinking degradable epoxy resin and preparation method and high-temperature leaking stoppage application thereof
A dynamic cross-linking, epoxy resin technology, applied in chemical instruments and methods, recycling technology, drilling composition, etc., can solve the problems of reducing mechanical properties, unable to meet the application requirements of high temperature leakage plugging, and achieve leakage protection layer effect
- Summary
- Abstract
- Description
- Claims
- Application Information
AI Technical Summary
Problems solved by technology
Method used
Examples
Embodiment 1
[0037] Weigh epoxy monomer E51 (50%), curing agent methylhexahydrophthalic anhydride-MHHPA (50%) and auxiliary agent zinc acetylacetonate-Zn(acac) in a beaker respectively 2 (10%), heated and stirred in an oil bath at 100°C, then mixed, poured into a mold, and put into an oven to cure at 100°C for 2 hours, 130°C for 2 hours, and 150°C for 2 hours; the glass transition of the obtained solid product The temperature was 150°C, and the temperature of 5% thermal weight loss was 300°C; the solid product sample was immersed in oil, aged in an oven at 180°C for 10 days, with a mass loss of 8.5%, and aged for 30 days with a mass loss of 80%.
[0038] The solid product was aged in an oven at 180°C for 10 days and 30 days; the unaged solid samples and aged samples were pulverized into particles as a plugging agent, and the plugging agent (8%) was mixed with calcium carbonate particles (15%, wherein , 10~20 mesh calcium carbonate 7%, 20~40 mesh calcium carbonate 4%, 40~80 mesh calcium car...
Embodiment 2
[0040] Same as Example 1, the difference is: the epoxy monomer (57%) adopted is E44 and 4.4-diaminodiphenylmethane tetraglycidylamine-TGDOM, and the curing agent is methylhexahydrophthalic anhydride-MHHPA (43 %), the auxiliary agent is zinc acetate-ZnAD (10%). The heating and curing process is as follows: curing at 60 °C for 1 hour, curing at 100 °C for 1 hour, curing at 130 °C for 2 hours, and curing at 150 °C for 2 hours.
[0041] The glass transition temperature of the solid product obtained in this example is 179°C, and the temperature at which 5% thermal weight loss occurs is 320°C; the solid product sample is immersed in oil, aged in an oven at 180°C for 10 days, with a mass loss of 4.5%, and aged for 30 days , with a mass loss of 73%.
[0042]The particle plugging agent (4%) of unaged, aged 10 days and 30 days samples was combined with calcium carbonate particles (8%), fibers (0.2%, 3~5mm, carbon fiber) and elastic graphite (4%), added Add the 4% bentonite base slurry...
Embodiment 3
[0044] Same as Example 1, the difference is: the epoxy monomer (50%) used is E51 and trimethylolpropane triglycidyl ether-TMTGE, and the auxiliary agent is zinc acetylacetonate-Zn(acac) 2 (2%). The heating and curing process is as follows: curing at 90 °C for 2 hours, curing at 120 °C for 1 hour, and curing at 150 °C for 4 hours.
[0045] The glass transition temperature of the solid product obtained in this example is 176°C, and the temperature at which the thermal weight loss is 5% is 300°C; the solid product sample is immersed in oil, aged in an oven at 180°C for 10 days, with a mass loss of 5.5%, and aged for 30 days , with a mass loss of 76%.
[0046] Unaged, aged 10 days, and 30 days samples of particulate loss-stopping agent (4%) were combined with calcium carbonate particles (12%), fibers (0.2%) and elastic graphite (6%), added to a 4% bentonite base slurry In the test slurry, the experimental slurry was formed; a long crack (3×2mm) plugging experimental device was u...
PUM
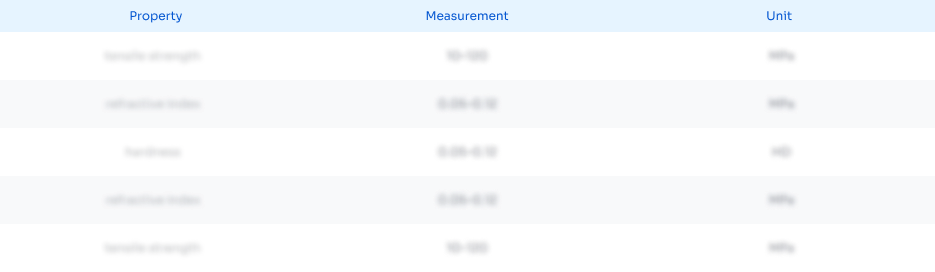
Abstract
Description
Claims
Application Information

- R&D
- Intellectual Property
- Life Sciences
- Materials
- Tech Scout
- Unparalleled Data Quality
- Higher Quality Content
- 60% Fewer Hallucinations
Browse by: Latest US Patents, China's latest patents, Technical Efficacy Thesaurus, Application Domain, Technology Topic, Popular Technical Reports.
© 2025 PatSnap. All rights reserved.Legal|Privacy policy|Modern Slavery Act Transparency Statement|Sitemap|About US| Contact US: help@patsnap.com