Composite robot operation system based on multi-sensor fusion
A technology of multi-sensor fusion and operation system, applied in the field of compound robot operation system, can solve the problems of hidden safety hazards, low positioning accuracy, and easy collision of industrial robots when moving.
- Summary
- Abstract
- Description
- Claims
- Application Information
AI Technical Summary
Problems solved by technology
Method used
Image
Examples
Embodiment Construction
[0040] Embodiments of the present disclosure will be described in more detail below with reference to the accompanying drawings. Although certain embodiments of the present disclosure are shown in the drawings, it should be understood that the disclosure may be embodied in various forms and should not be construed as limited to the embodiments set forth herein; A more thorough and complete understanding of the present disclosure. It should be understood that the drawings and embodiments of the present disclosure are for exemplary purposes only, and are not intended to limit the protection scope of the present disclosure.
[0041] It should be understood that the various steps described in the method implementations of the present disclosure may be executed in different orders, and / or executed in parallel. Additionally, method embodiments may include additional steps and / or omit performing illustrated steps. The scope of the present disclosure is not limited in this respect. ...
PUM
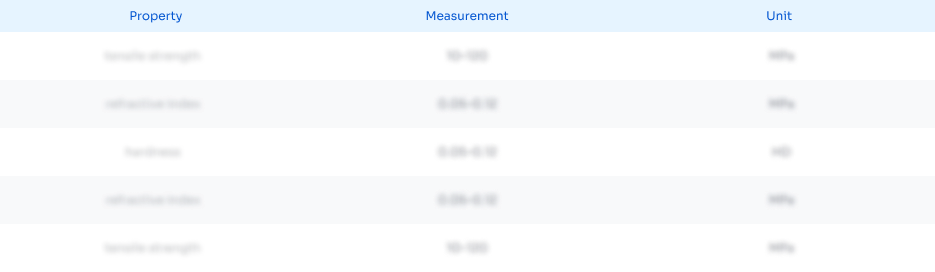
Abstract
Description
Claims
Application Information

- Generate Ideas
- Intellectual Property
- Life Sciences
- Materials
- Tech Scout
- Unparalleled Data Quality
- Higher Quality Content
- 60% Fewer Hallucinations
Browse by: Latest US Patents, China's latest patents, Technical Efficacy Thesaurus, Application Domain, Technology Topic, Popular Technical Reports.
© 2025 PatSnap. All rights reserved.Legal|Privacy policy|Modern Slavery Act Transparency Statement|Sitemap|About US| Contact US: help@patsnap.com