A kind of dynamic grating pattern generation method and system for 3D measurement
A dynamic grating and pattern technology, applied in the field of optics and electronics, can solve the problems of complex system, low optical utilization rate, low brightness, etc.
- Summary
- Abstract
- Description
- Claims
- Application Information
AI Technical Summary
Problems solved by technology
Method used
Image
Examples
Embodiment 1
[0059] as attached figure 1 to the attached Image 6 As shown, an embodiment of the present invention provides a dynamic grating pattern generation system for 3D measurement, including a light-emitting unit array 1 for emitting high-frequency stroboscopic light, and the light-emitting unit array 1 includes a number of parallel and spaced light-emitting units 11. Each light-emitting unit 11 can be independently controlled, and the number of light-emitting units 11 can be 50, 100, etc. The specific number is set according to the required resolution.
[0060] Define the plane where the light-emitting unit array 1 is located as the reference plane, with the X-axis direction and the Y-axis direction perpendicular to each other, and define the light propagation path as the Z-axis direction;
[0061] a lens array, arranged on the light propagation path, for focusing the light in the Y-axis direction, the lens array includes a plurality of lens units, and each lens unit corresponds t...
Embodiment 2
[0085] The difference between this embodiment and the first embodiment is that, as shown in the appendix Figure 7 As shown, a first optical element 7 is added in the light propagation path. The first optical element 7 is located between the lens array and the grating shaping array 3, and is used to collimate the light in the X-axis direction. The first optical element 7 can be A single cylindrical lens, or a group of cylindrical lenses, or a DOE (diffractive optical element).
[0086] In this embodiment, the light-emitting units 11 in the light-emitting unit array 1 are one or more point light sources or line light sources along the X-axis direction.
[0087] In order to ensure that the projected pattern on the working surface is in the shape of a grating strip, the length of the collimated beam should be greater than the length L of the light-transmitting area 31 in the grating shaping array 3 . When the light-emitting unit is a point light source, the focal length f of the...
Embodiment 3
[0091] The difference between this embodiment and the first embodiment is that, as shown in the appendix Figure 8 As shown, a second optical element 8 is added in the light propagation path. The second optical element 8 is located between the lens array and the grating shaping array 3 to change the divergence angle of the light in the X-axis direction, thereby controlling the working surface 6 The length of the projected pattern on the X axis. The second optical element 8 may be a single cylindrical lens, or a group of cylindrical lenses, or a DOE (Diffractive Optical Element).
[0092] Since the second optical element is added to constrain the divergence angle of light in the X-axis direction, the projection lens 5 in this embodiment can be composed of a cylindrical mirror, and only focuses the light beam passing through the grating shaping array 3 in the Y-axis direction, so that the The resulting grating strips are focused on the working surface 6 without changing the pro...
PUM
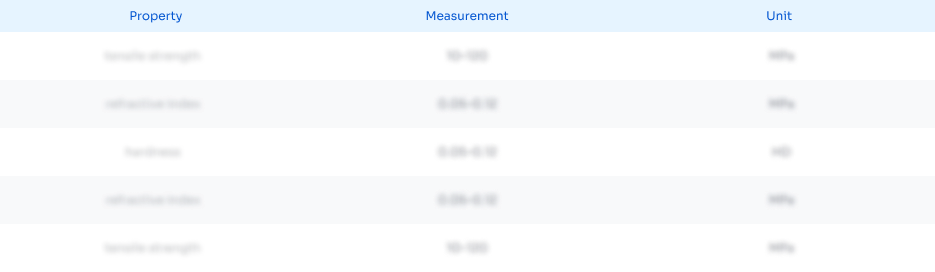
Abstract
Description
Claims
Application Information

- Generate Ideas
- Intellectual Property
- Life Sciences
- Materials
- Tech Scout
- Unparalleled Data Quality
- Higher Quality Content
- 60% Fewer Hallucinations
Browse by: Latest US Patents, China's latest patents, Technical Efficacy Thesaurus, Application Domain, Technology Topic, Popular Technical Reports.
© 2025 PatSnap. All rights reserved.Legal|Privacy policy|Modern Slavery Act Transparency Statement|Sitemap|About US| Contact US: help@patsnap.com