Support plate glass arraying device with damage sensing function and arraying method
A technology of alignment devices and sensing devices, applied in the field of carrier glass alignment devices, can solve problems such as breakage, broken glass, glass scratches, etc., and achieve the effects of improving production efficiency, reducing damage rate, and improving reliability
- Summary
- Abstract
- Description
- Claims
- Application Information
AI Technical Summary
Benefits of technology
Problems solved by technology
Method used
Image
Examples
Embodiment 1
[0066] The alignment auxiliary mechanism 2 includes a cylinder driving mechanism, a brush fixing device, and a brush.
[0067] The positioning sensing device 3 of the carrier glass and the auxiliary mechanism 2 for the alignment include a servo motor 31 , a connecting sleeve, a swing arm 321 , a polyurethane wheel 322 and a complete mechanism fixing frame. In the present invention, the contact wheel with the carrier glass 4 is made of polyurethane material, which has a certain buffer force and reduces the breakage rate of the glass.
[0068] The working principle and process of the present invention: the carrier glass 4 is transported to the designated position by the parallel multi-section belt conveyor 1, at this time, the alignment auxiliary mechanism 2 installed at the bottom of the belt conveyor 1 acts, and the cylinder 21 rises. The top brush 24 is in contact with the carrier glass 4 and acts as a buffer. At this time, the four positioning sensing devices 3 driven by th...
Embodiment 2
[0070] The application process of the present invention is as follows: when the carrier glass 4 is placed on the multi-line parallel belt conveyor 1 with holes, the belt 11 rotates to transport the carrier glass 4 to the position shown in the figure, and the alignment auxiliary mechanism 2 operates, and the cylinder 21 Lift up to lift the carrier glass 4, at this moment, the four positioning sensing devices 3 driven by the servo motor 31 act, and the swing arm 321 rotates 90° from the vertical position, so that the polyurethane wheel 322 at the front end of the swing arm 321 is in contact with the carrier plate. The distance between the glass 4 is 0.5mm. At this time, the servo motor 31 is changed from position control to torque control, and the polyurethane wheel 322 will continue to move close to the glass. At this time, the change of the encoder position value of the servo motor 31 is used to sense whether it is damaged. If the position value changes more than 1mm, it will a...
PUM
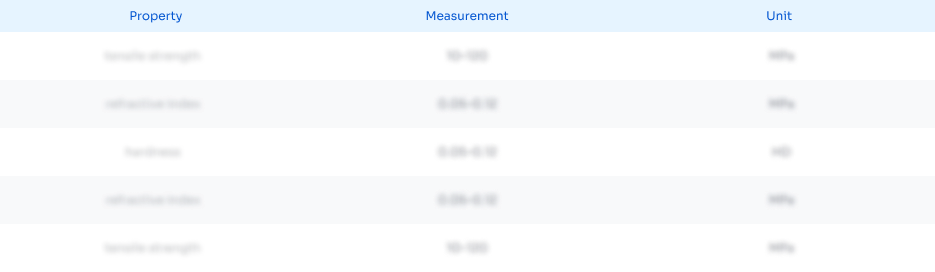
Abstract
Description
Claims
Application Information

- R&D
- Intellectual Property
- Life Sciences
- Materials
- Tech Scout
- Unparalleled Data Quality
- Higher Quality Content
- 60% Fewer Hallucinations
Browse by: Latest US Patents, China's latest patents, Technical Efficacy Thesaurus, Application Domain, Technology Topic, Popular Technical Reports.
© 2025 PatSnap. All rights reserved.Legal|Privacy policy|Modern Slavery Act Transparency Statement|Sitemap|About US| Contact US: help@patsnap.com