Inspection robot positioning method based on multi-sensor fusion
A multi-sensor fusion, inspection robot technology, applied in satellite radio beacon positioning systems, instruments, navigation through speed/acceleration measurement, etc. Guaranteed Robust and Accurate Effects
- Summary
- Abstract
- Description
- Claims
- Application Information
AI Technical Summary
Problems solved by technology
Method used
Image
Examples
Embodiment Construction
[0032] The present invention is further explained in detail below in conjunction with the accompanying drawings.
[0033] refer to figure 1 , a positioning method for inspection robots based on multi-sensor fusion, the steps are as follows:
[0034] Step S1, collecting multi-sensor data, including the absolute positioning information of the Beidou positioning system (BDS), the data of the encoder (Odom) and the data of the inertial measurement unit (IMU) in the inspection robot.
[0035] In the Beidou Positioning System (BDS), the data reference coordinate system is the World Geodetic System coordinate system (WGS84), and its data includes longitude, latitude, altitude, positioning standard deviation, timing, etc. However, in order to ensure the availability of data and the uniformity of measurement, it is necessary to unify the radian system of latitude and longitude into the distance unit, that is, the metric system. Therefore, it is necessary to convert the BDS measuremen...
PUM
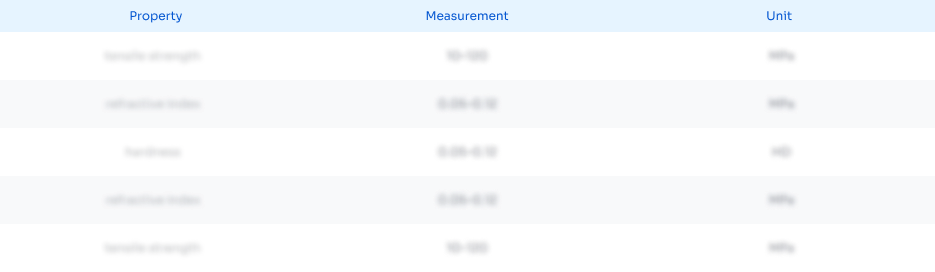
Abstract
Description
Claims
Application Information

- R&D
- Intellectual Property
- Life Sciences
- Materials
- Tech Scout
- Unparalleled Data Quality
- Higher Quality Content
- 60% Fewer Hallucinations
Browse by: Latest US Patents, China's latest patents, Technical Efficacy Thesaurus, Application Domain, Technology Topic, Popular Technical Reports.
© 2025 PatSnap. All rights reserved.Legal|Privacy policy|Modern Slavery Act Transparency Statement|Sitemap|About US| Contact US: help@patsnap.com