Apparatus and method for compact wire embedding welding using shaped electrodes
A compact technology for forming electrodes, applied in pressure electrodes, electrode features, welding equipment, etc., which can solve the problems of limited space for interconnecting wires, difficult and impossible crimping, etc.
- Summary
- Abstract
- Description
- Claims
- Application Information
AI Technical Summary
Problems solved by technology
Method used
Image
Examples
Embodiment Construction
[0037] The present invention will now be described more fully with reference to the accompanying drawings, in which exemplary embodiments of the invention are shown. However, this invention may be embodied in many different forms and should not be construed as limited to the embodiments set forth herein. Rather, these embodiments are provided so that this disclosure will be thorough and complete, and will fully convey the scope of the invention to those skilled in the art. Like numerals refer to like elements throughout.
[0038] As noted above, one problem associated with conventional techniques for resistance welding multi-strand cables 10 to much smaller diameter individual wires 20 is that it is difficult to maintain the position of thinner wires 20 during welding, as Figure 7 shown. In addition, due to the large diameter difference, the contact surface with the corresponding positive and negative welding electrodes is also different, such as Figure 7 indicated by the m...
PUM
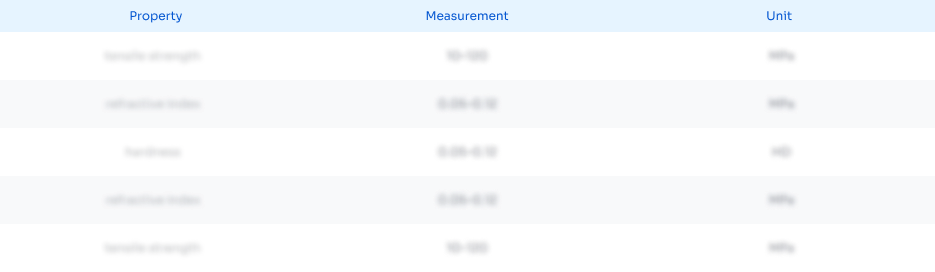
Abstract
Description
Claims
Application Information

- Generate Ideas
- Intellectual Property
- Life Sciences
- Materials
- Tech Scout
- Unparalleled Data Quality
- Higher Quality Content
- 60% Fewer Hallucinations
Browse by: Latest US Patents, China's latest patents, Technical Efficacy Thesaurus, Application Domain, Technology Topic, Popular Technical Reports.
© 2025 PatSnap. All rights reserved.Legal|Privacy policy|Modern Slavery Act Transparency Statement|Sitemap|About US| Contact US: help@patsnap.com