Remote intelligent control system and method for gantry crane
A portal crane and control system technology, applied in control/adjustment system, non-electric variable control, two-dimensional position/channel control, etc., can solve the problem that the portal crane cannot carry out multi-machine collaborative operation, and the driver can operate on the machine, etc. problems, to achieve the effect of improving the rate and efficiency of automation operations and reducing the risk of safety accidents
- Summary
- Abstract
- Description
- Claims
- Application Information
AI Technical Summary
Problems solved by technology
Method used
Image
Examples
Embodiment 1
[0045] Provide a remote intelligent control system for portal cranes, such as figure 1 As shown, wherein the system includes:
[0046] Data collection module 10, automatic control module 20, video surveillance module 30, intelligent control module 40 and remote operation module 50, data collection module 10, automatic control module 20, video surveillance module 30, remote operation module 50 are respectively connected with intelligent control Module 40 communication connection;
[0047] The data acquisition module 10 is used to collect the pose information of the operating mechanism of each portal crane and the ship type information of the operating vessel in real time through a plurality of peripheral sensing devices with different functions installed on the portal crane, and transmit the collected data to To the intelligent control module 40 in the central control room;
[0048] The automatic control module 20 includes a single-machine automatic operation system and a sin...
Embodiment 2
[0073] A method is provided, which adopts the remote intelligent control system of the portal crane as described in the first embodiment, which includes the following steps:
[0074] S1. Through multiple peripheral sensing devices with different functions installed on the portal cranes, the pose information of the operating mechanism of each portal crane and the ship type information of the operating vessel are collected in real time, and the collected data is transmitted to the intelligent control module in the central control room ;
[0075] S2. The intelligent control module issues operation tasks to each portal crane, and uses the single-machine automatic operation system to convert the operation instructions of each mechanism to realize the automatic operation of each portal crane;
[0076] S3. Through the cameras installed at key positions on each portal crane, the video signal is transmitted to the central control room for centralized display, realizing real-time safety...
PUM
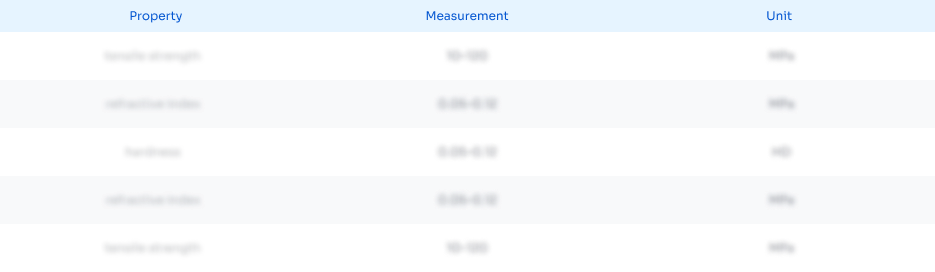
Abstract
Description
Claims
Application Information

- Generate Ideas
- Intellectual Property
- Life Sciences
- Materials
- Tech Scout
- Unparalleled Data Quality
- Higher Quality Content
- 60% Fewer Hallucinations
Browse by: Latest US Patents, China's latest patents, Technical Efficacy Thesaurus, Application Domain, Technology Topic, Popular Technical Reports.
© 2025 PatSnap. All rights reserved.Legal|Privacy policy|Modern Slavery Act Transparency Statement|Sitemap|About US| Contact US: help@patsnap.com