Forming method of high-frequency-vibration-resistant high-pressure gas cylinder wound with support
A high-pressure gas cylinder and molding method technology, which is applied to household components, household appliances, other household appliances, etc., can solve the problem that the bonding strength of metal connectors is difficult to reach the welding strength of metal gas cylinders, and the connection between the bottle body and the support is broken. , It is difficult to adapt to elastic deformation and other problems to achieve the effect of reducing negative quality, low cost and easy processing
- Summary
- Abstract
- Description
- Claims
- Application Information
AI Technical Summary
Problems solved by technology
Method used
Image
Examples
Embodiment Construction
[0022] pass below Figure 1 ~ Figure 2 As well as listing some optional embodiments of the present invention, the technical solutions (including preferred technical solutions) of the present invention are further described in detail. Apparently, the described embodiments are only some of the embodiments of the present invention, not all of them. Based on the embodiments of the present invention, all other embodiments obtained by persons of ordinary skill in the art without creative efforts fall within the protection scope of the present invention.
[0023] like figure 1 As shown, the anti-high-frequency vibration band support winding high-pressure gas cylinder forming method designed by the present invention is characterized in that it comprises the following steps:
[0024] S1. Before winding the gas cylinder, use ethyl acetate to scrub the surface of the inner liner 1. After standing for 5 minutes, apply 730 adhesive twice, with an interval of 15 minutes between each pass....
PUM
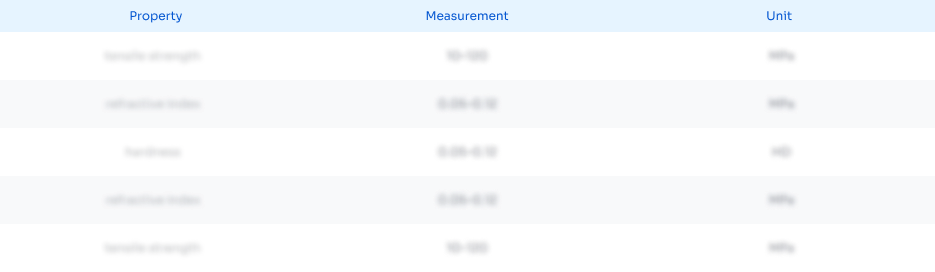
Abstract
Description
Claims
Application Information

- R&D
- Intellectual Property
- Life Sciences
- Materials
- Tech Scout
- Unparalleled Data Quality
- Higher Quality Content
- 60% Fewer Hallucinations
Browse by: Latest US Patents, China's latest patents, Technical Efficacy Thesaurus, Application Domain, Technology Topic, Popular Technical Reports.
© 2025 PatSnap. All rights reserved.Legal|Privacy policy|Modern Slavery Act Transparency Statement|Sitemap|About US| Contact US: help@patsnap.com